Oil slurry filtering device with two-stage filtration for catalytic cracking device
A catalytic cracking unit and secondary filtration technology, applied in the direction of filtration separation, filtration loop, gravity filter, etc., can solve the problems of high cost, short continuous operation period, and the filtration system cannot meet the basic requirements, so as to save costs and work. Time extension, the effect of prolonging the continuous operation time
- Summary
- Abstract
- Description
- Claims
- Application Information
AI Technical Summary
Problems solved by technology
Method used
Image
Examples
Embodiment 1
[0021] see figure 1 and figure 2 , the present invention's two-stage filtering catalytic cracking unit external oil slurry filtering device includes a series first-stage filter and a second-stage filter, the first-stage filter is one or two filters 1, and the second-stage Filtration is at least two filters 2; the filter element used in the filter 1 of the first stage filtration is a wedge-shaped wire wound filter element 11, and the wedge-shaped wire wound filter element 11 is composed of a wedge-shaped metal wire winding, and each circle of wire According to the size distribution of the solid catalyst particles in the oil slurry, select an appropriate size for the gap between the adjacent metal wires, the range is 10-50 microns, and the options are 10 microns, 15 microns, 20 microns, 25 microns, and 30 microns , 35 microns, 40 microns, 45 microns or 50 microns and other different sizes, and is a continuous funnel shape; the filter 2 of the second-stage filtration uses a met...
Embodiment 2
[0023] Embodiment 2: the operation process embodiment of primary filter
[0024]The primary filter starts working when the filter to be protected is about to be backwashed off-line. The oil slurry enters the filter from the bottom of the filter 1, and the oil slurry flows out from the filtrate outlet 13 of the filter by wrapping the outside of the filter core 11 by a wedge-shaped wire under the action of pressure. Most of the solid catalyst particles will form a filter cake on the outer surface of the wedge wire wound filter element 11 . Filtration online cycle time can be set. When the predetermined filter cake is formed, the pre-filter stops working, and the filter cake is cleaned with recycled oil. When the first stage filter 1 completes the backwashing and starts working again, the oil slurry will first pass through the first stage filter 1 to intercept the asphaltene and particles that cannot penetrate the filter cake on the first stage filter 1, some of which are small...
Embodiment 3
[0025] Embodiment 3: Secondary filter operation process embodiment
[0026] The filtration process occurs when the oil slurry (from under the tube sheet) flows into the filter and passes through the metal powder sintered filter element 3 . Solids (catalyst powder) are trapped outside the surface of the filter element to form a filter cake due to their size larger than the pore size. The clean oil slurry flows through the filter cake layer, passes through the metal powder sintered filter element 3, and flows out of the filter as clean filtered oil.
[0027] During the filtration process, the filter cake will gradually thicken and the flow resistance will gradually increase. The set flow rate is maintained by increasing the pressure difference between the inner and outer walls of the filter element. In this way, the filtration continues until the final filter element pressure difference reaches the set value or reaches the set maximum filtration time, then the filter must be b...
PUM
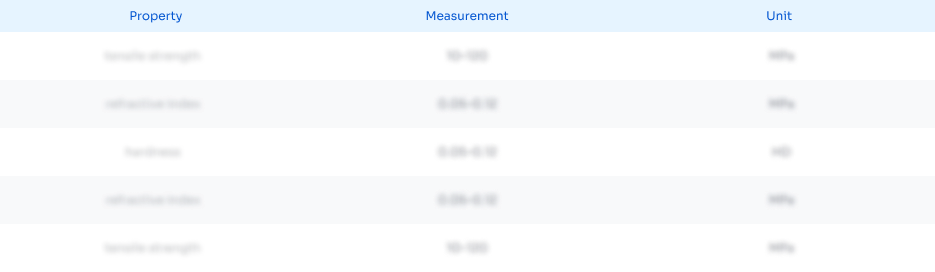
Abstract
Description
Claims
Application Information

- R&D
- Intellectual Property
- Life Sciences
- Materials
- Tech Scout
- Unparalleled Data Quality
- Higher Quality Content
- 60% Fewer Hallucinations
Browse by: Latest US Patents, China's latest patents, Technical Efficacy Thesaurus, Application Domain, Technology Topic, Popular Technical Reports.
© 2025 PatSnap. All rights reserved.Legal|Privacy policy|Modern Slavery Act Transparency Statement|Sitemap|About US| Contact US: help@patsnap.com