Super wear-resistant rubber-plastic conveyer belt
A conveyor belt, ultra-wear-resistant technology, applied in the field of conveyor belts, can solve the problems of inner core wear and damage, poor wear resistance of cover rubber, affecting the quality and service life of rubber conveyor belts, and achieve good low-temperature performance.
- Summary
- Abstract
- Description
- Claims
- Application Information
AI Technical Summary
Problems solved by technology
Method used
Examples
Embodiment 1
[0014] First, take 40 parts by weight of natural rubber and masticate at 40°C for 20 minutes; place the masticated rubber at 20°C for 8 hours; then mix 65 parts by weight of butadiene rubber and 3 parts by weight High styrene, 65 parts by weight of high wear-resistant carbon black, 4 parts by weight of No. 40 motor oil, 1.0 parts by weight of antioxidant D, 1.2 parts by weight of antioxidant A, 1.5 parts by weight of antioxidant 4010NA, 3.0 parts by weight Zinc oxide, 2.0 parts by weight of stearic acid, and 1.2 parts by weight of accelerator NOBS were added to the internal mixer for mixing at 130°C for 20 minutes; the raw material after the internal mixing was added with 2.2 parts by weight of sulfur, After mixing at a temperature of 45°C, the sheet is loaded according to the specifications; the specifications of the conveyor belt material are vulcanized at a temperature of 150°C and a pressure of 15Mpa for 20 minutes to obtain a super wear-resistant rubber-plastic conveyor bel...
Embodiment 2
[0016] First, take 45 parts by weight of natural rubber and masticate at a temperature of 50°C for 25 minutes; place the masticated rubber at room temperature at 25°C for 9 hours; then mix 55 parts by weight of butadiene rubber and 6 parts by weight High styrene, 68 parts by weight of high wear-resistant carbon black, 5 parts by weight of No. 40 motor oil, 1.2 parts by weight of antioxidant D, 1.5 parts by weight of antioxidant A, 1.2 parts by weight of antioxidant 4010NA, 3.2 parts by weight Zinc oxide, 1.8 parts by weight of stearic acid, and 1.3 parts by weight of accelerator NOBS were added to the internal mixer for mixing at a temperature of 135°C for 15 minutes; 2.5 parts by weight of sulfur was added to the raw material after the banburying process. After mixing at a temperature of 40°C, the sheet is loaded according to the specifications; the specifications of the conveyor belt material are vulcanized at a temperature of 145°C and a pressure of 16Mpa for 25 minutes to ob...
Embodiment 3
[0018] First, take 43 parts by weight of natural rubber and masticate at 55°C for 22 minutes; place the masticated rubber at 22°C for 10 hours; then mix 60 parts by weight of butadiene rubber and 6 parts by weight. High styrene, 70 parts by weight of high wear-resistant carbon black, 3 parts by weight of No. 40 motor oil, 1.5 parts by weight of antioxidant D, 1.0 parts by weight of antioxidant A, 1.0 parts by weight of antioxidant 4010NA, 3.5 parts by weight Zinc oxide, 1.6 parts by weight of stearic acid, 1.4 parts by weight of accelerator NOBS were added to the internal mixer and mixed at a temperature of 133°C for 17 minutes; the raw material after the banbury was added with 2.0 parts by weight of sulfur and sulfur. After mixing at a temperature of 43°C, the sheet is loaded according to the specifications; the specifications of the conveyor belt material are vulcanized at a temperature of 140°C and a pressure of 17Mpa for 22 minutes to obtain a super wear-resistant rubber-pla...
PUM
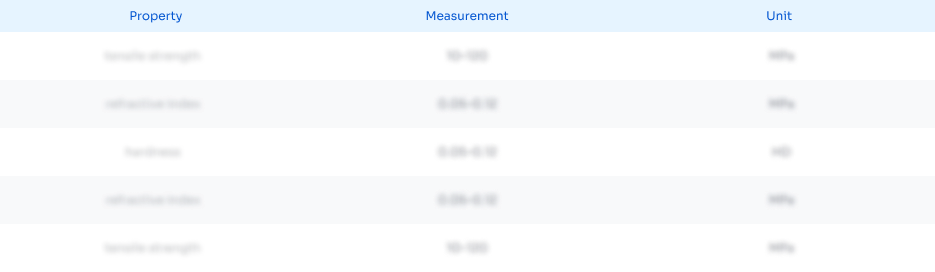
Abstract
Description
Claims
Application Information

- R&D Engineer
- R&D Manager
- IP Professional
- Industry Leading Data Capabilities
- Powerful AI technology
- Patent DNA Extraction
Browse by: Latest US Patents, China's latest patents, Technical Efficacy Thesaurus, Application Domain, Technology Topic, Popular Technical Reports.
© 2024 PatSnap. All rights reserved.Legal|Privacy policy|Modern Slavery Act Transparency Statement|Sitemap|About US| Contact US: help@patsnap.com