Method for continuously preparing poly-sulphur
A technology for polymerizing sulfur and sulfur, applied in the preparation/purification of sulfur, etc., can solve the problems of environmental pollution, carbon disulfide emission, low flash point and boiling point of carbon disulfide, etc., and achieve the effect of high safety factor and low energy consumption
- Summary
- Abstract
- Description
- Claims
- Application Information
AI Technical Summary
Benefits of technology
Problems solved by technology
Method used
Image
Examples
Embodiment
[0018] Preferred purity is more than 99.9% solid or liquid sulfur, it is heated up to 580~690 ℃, the mass ratio is 98.0~99.9: 0.1~2.0 carbon disulfide and unsaturated olefin mixed solvent temperature is controlled at 40~60 ℃, by The high-temperature sulfur sent from the heater at 800-1000 kg / hour and the mixed solvent sent from the circulating tank at 8000-20000 kg / hour are quenched (that is, quenched) in the synthesizer; the quenched mixture continuously enters the primary solidification In the device, keep the inclined primary curing device with the lifting plate at a speed of 0.1 to 3.0 circles per minute, and at the same time keep the liquid level of the primary curing device at 100 to 500mm below the position of the feed inlet, and keep the solid material after quenching at all times. It is in the liquid material and is continuously and slowly conveyed to the lower end of the primary curing device under the push of the copying board. The material is cured at one time durin...
PUM
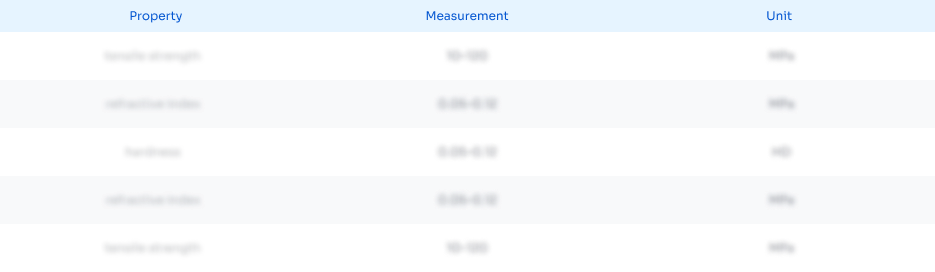
Abstract
Description
Claims
Application Information

- Generate Ideas
- Intellectual Property
- Life Sciences
- Materials
- Tech Scout
- Unparalleled Data Quality
- Higher Quality Content
- 60% Fewer Hallucinations
Browse by: Latest US Patents, China's latest patents, Technical Efficacy Thesaurus, Application Domain, Technology Topic, Popular Technical Reports.
© 2025 PatSnap. All rights reserved.Legal|Privacy policy|Modern Slavery Act Transparency Statement|Sitemap|About US| Contact US: help@patsnap.com