Detoxifying method of chlorine trifluoride
A chlorine trifluoride, fluorine gas technology, applied in chemical instruments and methods, separation methods, gas treatment and other directions, can solve the problems of difficult separation or concentration, difficult to remove, etc.
- Summary
- Abstract
- Description
- Claims
- Application Information
AI Technical Summary
Problems solved by technology
Method used
Image
Examples
Embodiment 1
[0047] The temperature of the outer wall of the nickel cylindrical reactor 3 with an inner diameter of 30 mm and a length of 600 mm is set to 350° C., and a mass flow controller 1 is used to introduce 2.8 mol% of Fluorine and 3.5mol% ClF 3 and use mass flow controller 2 to introduce 3.4mol% chlorine gas at a flow rate of 10ml / min, make it react for 30 seconds, and then pass through the water scrubber (exhaust gas treatment device) connected to the rear stage 5 and the scrubber (exhaust gas treatment device) 6 of the alkaline solution whose KOH concentration is 0.1mol / l carry out detoxification treatment, then, the outlet gas that the scrubber circulates is sampled, using FT-IR (manufactured by Otsuka Electronics Co., Ltd. IG-1000) to ClO3 The concentration of F was analyzed and the result was 180 volppm.
Embodiment 2
[0051] The temperature of the outer wall of the nickel cylindrical reactor 3 with an inner diameter of 12.4mm and a length of 1000mm is set to 350°C, and a mass flow controller 1 is used to introduce 5.0mol% Fluorine gas and 3.0mol% ClF 3 and use the mass flow controller 2 to introduce 6.0mol% chlorine to it at a flow rate of 44ml / min, make it react for 30 seconds, then pass through the water scrubber (exhaust gas treatment device) connected to the rear stage 5 and the scrubber (exhaust gas treatment device) 6 of the alkaline solution whose KOH concentration is 0.1mol / l carry out detoxification treatment, then, the outlet gas that the scrubber circulates is sampled, using FT-IR (manufactured by Otsuka Electronics Co., Ltd. IG-1000) to ClO 3 The concentration of F was analyzed and the result was 4 volppm.
Embodiment 3
[0055] The temperature of the outer wall of the nickel cylindrical reactor 3 with an inner diameter of 30 mm and a length of 600 mm is set to 370° C., and a mass flow controller 1 is used to introduce 2.8 mol% of Fluorine and 3.5mol% ClF 3 and use mass flow controller 2 to introduce 3.4mol% chlorine gas at a flow rate of 10ml / min, make it react for 30 seconds, and then pass through the water scrubber (exhaust gas treatment device) connected to the rear stage 5 and the scrubber (exhaust gas treatment device) 6 of the alkaline solution whose KOH concentration is 0.1mol / l carry out detoxification treatment, then, the outlet gas that the scrubber circulates is sampled, using FT-IR (manufactured by Otsuka Electronics Co., Ltd. IG-1000) to ClO 3 The concentration of F was analyzed and the result was 160 volppm.
PUM
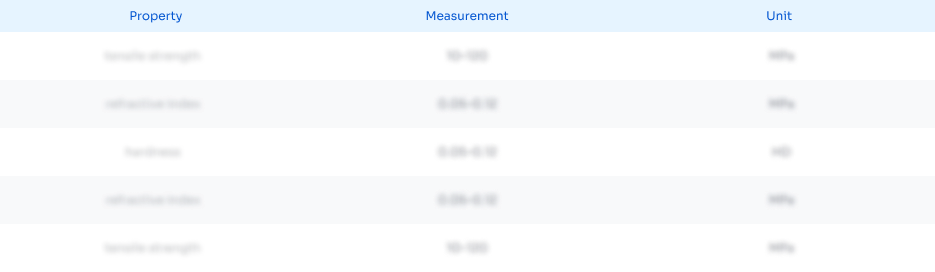
Abstract
Description
Claims
Application Information

- Generate Ideas
- Intellectual Property
- Life Sciences
- Materials
- Tech Scout
- Unparalleled Data Quality
- Higher Quality Content
- 60% Fewer Hallucinations
Browse by: Latest US Patents, China's latest patents, Technical Efficacy Thesaurus, Application Domain, Technology Topic, Popular Technical Reports.
© 2025 PatSnap. All rights reserved.Legal|Privacy policy|Modern Slavery Act Transparency Statement|Sitemap|About US| Contact US: help@patsnap.com