High-gravity (g) acceleration sensor in plane of micro-electromechanical system (MEMS) based on resonance tunnelling structure (RTS)
An acceleration sensor, silicon-based technology, applied in the field of MEMS sensors, can solve the problems that detection results are easily affected by temperature, difficult to integrate sensors in three axes, difficult to measure acceleration, etc., and achieve good resistance to high overload, good sensitivity, and not easy to fail. Effect
- Summary
- Abstract
- Description
- Claims
- Application Information
AI Technical Summary
Problems solved by technology
Method used
Image
Examples
Embodiment Construction
[0020] Such as figure 1 As shown, the RTS-based MEMS in-plane high-g acceleration sensor includes a silicon-based frame 1, a mass block 2 suspended in the silicon-based frame 1, and one side of the mass block 2 is fixed to the silicon-based frame 1 by an independent support beam 3. The opposite side is fixed to the silicon-based frame 1 by two parallel composite beams, the independent support beam 3 is parallel to the composite beam, and the independent support beam 3 is arranged along the center line of the mass block 2, and the two composite beams take the center line of the mass block 2 as the axis of symmetry Symmetrically arranged; the composite beam includes a detection beam 5 and two connecting beams 4 respectively arranged at both ends of the detection beam 5 to realize the fixing of the detection beam 5 and the quality block 2 and the silicon-based frame 1. The detection beam 5 is provided with a strain compressive force Sensitive element 6, the thickness and width of...
PUM
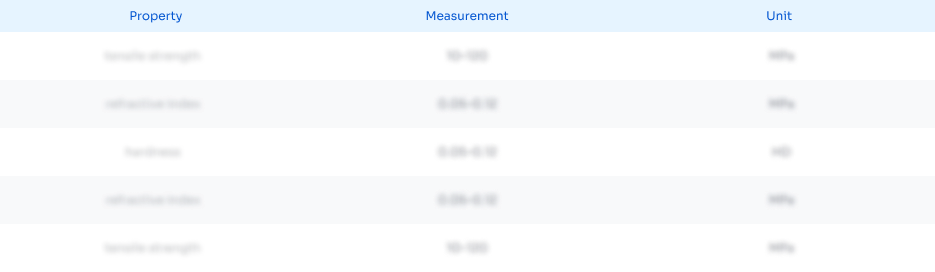
Abstract
Description
Claims
Application Information

- Generate Ideas
- Intellectual Property
- Life Sciences
- Materials
- Tech Scout
- Unparalleled Data Quality
- Higher Quality Content
- 60% Fewer Hallucinations
Browse by: Latest US Patents, China's latest patents, Technical Efficacy Thesaurus, Application Domain, Technology Topic, Popular Technical Reports.
© 2025 PatSnap. All rights reserved.Legal|Privacy policy|Modern Slavery Act Transparency Statement|Sitemap|About US| Contact US: help@patsnap.com