Industrial robot control system based on visual positioning and control method thereof
An industrial robot and visual positioning technology, applied in the field of robotics, can solve the problems of high requirements on the accuracy of robot models and tool coordinate system parameters, cannot meet the needs of high-precision complex trajectory operations, and the online teaching operation process is cumbersome. To achieve the effect of simple structure, reliable fixation and convenient operation
- Summary
- Abstract
- Description
- Claims
- Application Information
AI Technical Summary
Problems solved by technology
Method used
Image
Examples
Embodiment 1
[0038] Figure 1 to Figure 6 It is the vision positioning based industrial robot control system and its control method described in Embodiment 1. The industrial robot control system such as figure 1 As shown, the system includes a robot 1, a robot controller 2 and a visual measuring device, the visual measuring device is a binocular visual measuring device 3, the robot 1 adopts a six-axis robot, and the end is provided with an operating tool 5, and the robot 1 passes the robot The controller 2 is connected with the binocular vision measuring device 3, and the robot controller 2 uses the positioning information of the binocular vision measuring device 3 as feedback information. The luminous marking point 4 is fixed on the operating tool 5 of the robot, and the binocular vision measuring device 3 measures the luminous marking point 4 in real time, and the movement trajectory of the robot end operation tool can be determined by measuring the luminous marking point. The binocula...
Embodiment 2
[0061] Such as Figure 7 As shown, the difference from Embodiment 1 is that five luminescent marking points are fixed on the operating tool, which are respectively the first marking point 4A, the second marking point 4B, the third marking point 4C, and the fourth marking point 4D. and fifth marking point 4E. The connecting line between the first marking point 4A and the second marking point 4B is perpendicular to the connecting line between the third marking point 4C and the fourth marking point 4D and intersects at a point, and the fifth marking point 4E is located at the intersection point. The more markers distributed, the less impact a single illuminated marker will have on motion accuracy.
[0062] Others are with embodiment 1.
Embodiment 3
[0064] Such as Figure 8 As shown, the difference from Embodiment 1 is that the operating tool is fixed with six luminous marking points, which are respectively the first marking point 4A, the second marking point 4B, the third marking point 4C, and the fourth marking point 4D. , the fifth marking point 4E and the sixth marking point 4F. Wherein the connecting line of the first marking point 4A, the second marking point 4B is perpendicular to the connecting line of the third marking point 4C and the fourth marking point 4D, and intersects at one point, the fifth marking point 4E is located on the intersection point, the sixth The marking point 4F is located directly below the second marking point 4B.
PUM
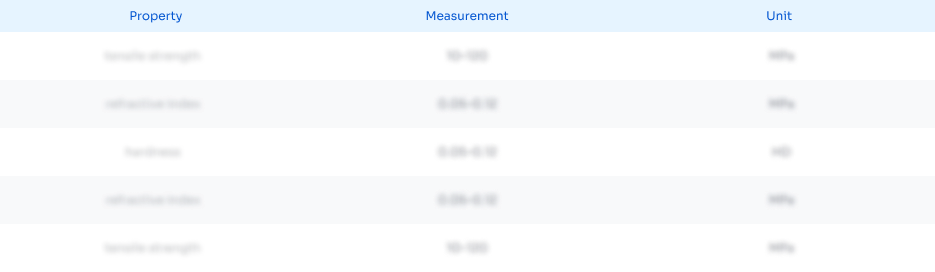
Abstract
Description
Claims
Application Information

- R&D
- Intellectual Property
- Life Sciences
- Materials
- Tech Scout
- Unparalleled Data Quality
- Higher Quality Content
- 60% Fewer Hallucinations
Browse by: Latest US Patents, China's latest patents, Technical Efficacy Thesaurus, Application Domain, Technology Topic, Popular Technical Reports.
© 2025 PatSnap. All rights reserved.Legal|Privacy policy|Modern Slavery Act Transparency Statement|Sitemap|About US| Contact US: help@patsnap.com