Heat transfer production process of silk socks
A production process and thermal transfer printing technology, which is applied in printing, transfer partial treatment, copying/marking methods, etc., can solve the problems that thermal transfer cannot be used, and stockings are not resistant to high temperature, etc.
- Summary
- Abstract
- Description
- Claims
- Application Information
AI Technical Summary
Problems solved by technology
Method used
Image
Examples
Embodiment Construction
[0011] The part in bold below is the process setting, that is, the specific implementation method of the present application, and the non-bold font is the production operation process, which is used for auxiliary explanation.
[0012] The key of this machine is to divide the original one-step work into two steps, to preheat the stockings to be transferred in advance, to remove the water on the surface of the stockings and to iron the transfer surface in the preheating part, and to preheat the stockings Raising the temperature, in the ensuing transfer process, can shorten the transfer time and reduce the temperature of the heat roller, so that the heat transfer can be completed without damaging the socks.
[0013] Referring to the accompanying drawings, this embodiment consists of a transfer part, a preheating part, and action time and pressure:
[0014] Transfer part: the transfer film 1 is wound on the transfer film unwinding frame 2, the transfer film 1 goes around the surfa...
PUM
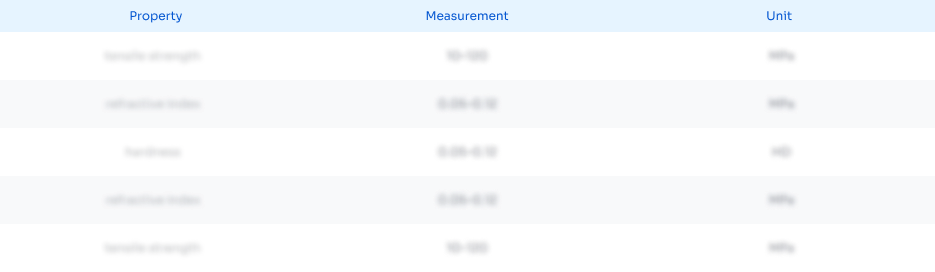
Abstract
Description
Claims
Application Information

- R&D
- Intellectual Property
- Life Sciences
- Materials
- Tech Scout
- Unparalleled Data Quality
- Higher Quality Content
- 60% Fewer Hallucinations
Browse by: Latest US Patents, China's latest patents, Technical Efficacy Thesaurus, Application Domain, Technology Topic, Popular Technical Reports.
© 2025 PatSnap. All rights reserved.Legal|Privacy policy|Modern Slavery Act Transparency Statement|Sitemap|About US| Contact US: help@patsnap.com