Casting method of aluminum alloy rod parts and casting equipment for realizing same
An aluminum alloy and equipment technology, applied in the casting field of aluminum alloy parts, can solve problems such as poor quality consistency of blanks, inability to fill local cavities, increase energy consumption of molten metal, etc., so as to improve product manufacturing efficiency, good solidification consistency, The effect of eliminating air slag holes
- Summary
- Abstract
- Description
- Claims
- Application Information
AI Technical Summary
Problems solved by technology
Method used
Image
Examples
Embodiment Construction
[0022] The method of the present invention adopts a casting method in which liquid is supplied under the liquid surface and the molten metal is cooled and solidified sequentially from bottom to top. The infusion tube is connected to the bottom of the container and inserted into the bottom of the mold cavity, and the molten metal is injected into the cavity through the infusion tube. The metal liquid overflows the liquid outlet at the bottom of the infusion tube to form a submerged liquid supply. The premise is that it is located below the liquid metal liquid level and gradually rises relative to the bottom of the cavity, and the liquid metal liquid level gradually rises relative to the bottom of the cavity and is sequentially cooled and solidified from the bottom to the top of the cavity.
[0023] Specific embodiments of the present invention will be described in detail below in conjunction with the accompanying drawings.
[0024] Such as figure 1 , figure 2 As shown, the c...
PUM
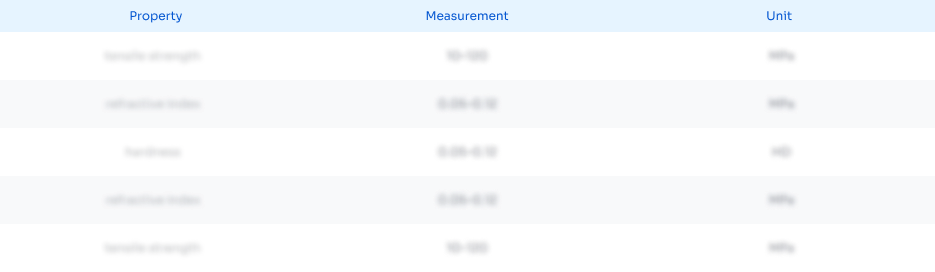
Abstract
Description
Claims
Application Information

- Generate Ideas
- Intellectual Property
- Life Sciences
- Materials
- Tech Scout
- Unparalleled Data Quality
- Higher Quality Content
- 60% Fewer Hallucinations
Browse by: Latest US Patents, China's latest patents, Technical Efficacy Thesaurus, Application Domain, Technology Topic, Popular Technical Reports.
© 2025 PatSnap. All rights reserved.Legal|Privacy policy|Modern Slavery Act Transparency Statement|Sitemap|About US| Contact US: help@patsnap.com