Method for extracting vanadium through composite blowing of converter
A converter and nitrogen technology, applied in the manufacture of converters, etc., can solve problems such as the inability to meet the kinetic conditions of the blowing process, the difficulty in achieving mutual coordination of vanadium extraction, and the adverse effects of steelmaking operations, so as to improve oxygen utilization and meet The needs of thermodynamic conditions and kinetic conditions, the effect of improving economic and technical indicators
- Summary
- Abstract
- Description
- Claims
- Application Information
AI Technical Summary
Problems solved by technology
Method used
Image
Examples
Embodiment 1
[0034] Vanadium extraction furnace 1:
[0035] The main components of vanadium-containing molten iron are C: 4.78%, Si+Ti: 0.82%, Mn: 0.18%, V: 0.258%, and the molten iron temperature is 1265°C. According to the above molten iron conditions, set the oxygen flow rate to 5550 m3 / h and nitrogen flow rate It is 18500m3 / h, the flow ratio of oxygen and nitrogen is 0.3, and the gas pressure after mixing is 1.2MPa. Put vanadium-containing molten iron into the converter. After the converter is shaken, the oxygen lance is lowered to the blowing position to start gas supply. After the oxygen gun is lowered to the oxygen opening point, first open the nitrogen regulating valve, and then open the oxygen regulating valve after the nitrogen flow reaches 18500m3 / h, so that oxygen and nitrogen are simultaneously supplied to the molten pool to achieve composite injection to the molten pool. During the blowing process, uniformly add loose coolants such as iron oxide skin balls, cold-solid pellets, ...
Embodiment 2
[0037] Vanadium extraction furnace 2:
[0038] The main components of vanadium-containing molten iron are C: 4.35%, Si+Ti: 0.24%, Mn: 0.20%, V: 0.333%, and molten iron temperature is 1272℃. According to the above molten iron conditions, set the oxygen flow rate to 10500 m3 / h and nitrogen flow rate It is 3500m3 / h, the flow ratio of oxygen and nitrogen is 3.0, and the gas pressure after mixing is 0.7MPa. Put vanadium-containing molten iron into the converter. After the converter is shaken, the oxygen lance is lowered to the blowing position to start gas supply. After the oxygen lance is lowered to the open oxygen point, first open the nitrogen regulating valve, and then open the oxygen regulating valve after the nitrogen flow reaches 3500m3 / h, so that oxygen and nitrogen are simultaneously supplied to the molten pool to achieve composite injection to the molten pool. During the blowing process, uniformly add loose coolants such as iron oxide skin balls, cold-solid pellets, hot-pre...
Embodiment 3
[0040] Vanadium extraction furnace 3:
[0041] The main components of vanadium-containing molten iron are C: 4.52%, Si+Ti: 0.55%, Mn: 0.14%, V: 0.288%, and the molten iron temperature is 1270℃. According to the above molten iron conditions, set the oxygen flow rate to 8500 m3 / h and nitrogen flow rate It is 8500m3 / h, the ratio of oxygen to nitrogen flow rate is 1.0, and the gas pressure after mixing is 0.85MPa. Put vanadium-containing molten iron into the converter. After the converter is shaken, the oxygen lance is lowered to the blowing position to start gas supply. After the oxygen lance drops to the oxygen opening point, first open the nitrogen regulating valve, and then open the oxygen regulating valve after the nitrogen flow reaches 8500m3 / h, so that oxygen and nitrogen are simultaneously supplied to the molten pool to achieve composite injection to the molten pool. During the blowing process, uniformly add loose coolants such as iron oxide skin balls, cold-solid pellets, h...
PUM
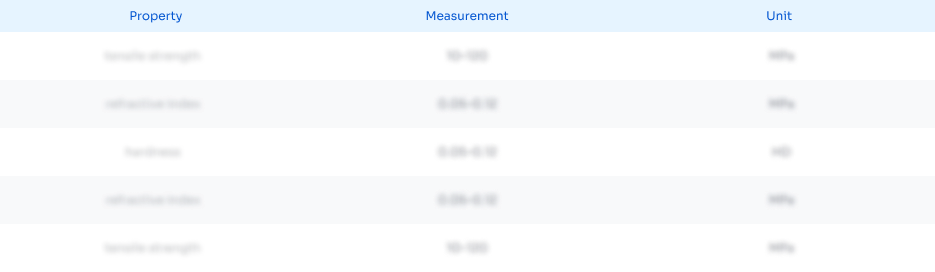
Abstract
Description
Claims
Application Information

- R&D
- Intellectual Property
- Life Sciences
- Materials
- Tech Scout
- Unparalleled Data Quality
- Higher Quality Content
- 60% Fewer Hallucinations
Browse by: Latest US Patents, China's latest patents, Technical Efficacy Thesaurus, Application Domain, Technology Topic, Popular Technical Reports.
© 2025 PatSnap. All rights reserved.Legal|Privacy policy|Modern Slavery Act Transparency Statement|Sitemap|About US| Contact US: help@patsnap.com