Light ageing resistant blend for composite insulator and preparation method thereof
A technology for composite insulators and light aging resistance, which is applied in the field of preparation of compounded rubber for composite insulators, and can solve the problems of decreased hydrophobicity, high strength, flashover accidents, etc.
- Summary
- Abstract
- Description
- Claims
- Application Information
AI Technical Summary
Problems solved by technology
Method used
Image
Examples
Embodiment 1
[0032] refer to figure 1 And Table 1, Table 1 lists the raw material proportions (parts by weight) of this embodiment, wherein the silicone rubber raw rubber is methyl vinyl silicone rubber, and its vinyl content is 0.04-0.12%. The method for preparing the mixed rubber for light-aging resistant composite insulators according to the ratio of raw materials in Table 1 comprises the following steps:
[0033] The pretreatment of step D, ultraviolet absorber UV-531, its method is: drop into raw silicone rubber, ultraviolet absorber UV-531 and methyl silicone oil in the kneader, silicone rubber raw rubber and ultraviolet absorber UV-531 The ratio is 100:40, a small amount of methyl silicone oil, after kneading for 60-80 minutes, the material is discharged, and the pasty ultraviolet absorber UV-531 is obtained after passing through the mill for 3 to 5 times. 0.2 ~ 0.5mm. As a release agent, methyl silicone oil can prevent raw silicone rubber and UV absorber UV531 from adhering to th...
Embodiment 2
[0045] refer to figure 1And Table 2, Table 2 lists the raw material ratio (parts by weight) of this embodiment, wherein the raw silicone rubber is methyl vinyl silicone rubber, and its vinyl content is 0.13-0.20%. The method for preparing the mixed rubber for light aging resistant composite insulators according to the ratio of raw materials in Table 2, the steps are the same as those in Example 1, the difference is that the weight of raw materials put into each step is different, the specific difference is:
[0046] Step D: pretreatment UV absorber UV-531, drop into raw silicone rubber, UV absorber UV-531 and methyl silicone oil in the kneader, wherein the ratio of raw silicone rubber to UV absorber UV-531 is 100: 50, a small amount of methyl silicone oil, after kneading for 60-80 minutes, the material is discharged, and the pasty ultraviolet absorber UV-531 is obtained after passing through the mill for 3-5 times, and the roll distance of the mill is 0.2-0.5 mm.
[0047] St...
Embodiment 3
[0053] refer to figure 1 And Table 3, Table 3 lists the raw material proportions (parts by weight) of this embodiment, wherein the silicone rubber raw rubber is methyl vinyl silicone rubber, and its vinyl content is 0.21-0.24%. The method for preparing the mixed rubber for light aging resistant composite insulators according to the ratio of raw materials in Table 3, the steps are the same as in Example 1, the difference is that the weight of raw materials put into each step is different, the specific difference is:
[0054] Step D: Pretreatment UV absorber UV-531, drop into raw silicone rubber, UV absorber UV-531 and methyl silicone oil in the kneader, wherein the ratio of raw silicone rubber to UV absorber UV-531 is 100: 60, a small amount of methyl silicone oil, after kneading for 60-80 minutes, the material is discharged, and the pasty ultraviolet absorber UV-531 is obtained after passing through the mill for 3-5 times, and the roll distance of the mill is 0.2-0.5 mm.
[...
PUM
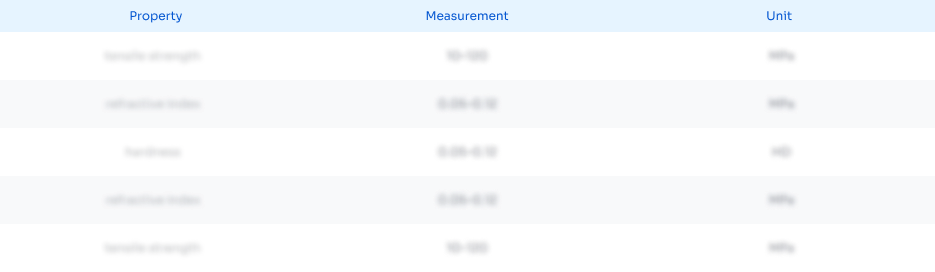
Abstract
Description
Claims
Application Information

- R&D
- Intellectual Property
- Life Sciences
- Materials
- Tech Scout
- Unparalleled Data Quality
- Higher Quality Content
- 60% Fewer Hallucinations
Browse by: Latest US Patents, China's latest patents, Technical Efficacy Thesaurus, Application Domain, Technology Topic, Popular Technical Reports.
© 2025 PatSnap. All rights reserved.Legal|Privacy policy|Modern Slavery Act Transparency Statement|Sitemap|About US| Contact US: help@patsnap.com