Method for preparing functional soybean polysaccharide based on Maillard reaction
A Maillard reaction and soybean polysaccharide technology, which is applied in the field of soybean polysaccharide preparation, can solve the problems of lack of clear analysis and discussion, difficult dispersion stability of soybean polysaccharide, etc., and achieves widening the range of functional applications, superior functionality, and reducing environmental pollution. Effect
- Summary
- Abstract
- Description
- Claims
- Application Information
AI Technical Summary
Problems solved by technology
Method used
Examples
Embodiment 1
[0019] In this embodiment, the dried okara produced as a by-product during the production of soybean protein isolate is used as a raw material. First, water 20 times the volume of the dried okara is added to the weighed dry okara, and the okara solution is formed under sufficient stirring; Hydrochloric acid is added dropwise to the bean dregs solution to adjust the pH value of the solution to 5, and it is cooked at a temperature of 150° C. in a high-temperature and high-pressure airtight container for 1 hour to form a soybean fiber decomposition liquid.
[0020] Then, extract the soybean fiber decomposition solution, quickly cool it down to 80°C within 0.5h, then add phosphate buffer solution dropwise to the solution to adjust its pH value to 6.5; continue to keep warm for 3h to produce Maillard reaction, so that the raw material The ε-amino group of the protein in the protein is further combined with the reducing carbonyl end of the polysaccharide in the soybean fiber decompos...
Embodiment 2
[0023] In this example, the dried okara produced as a by-product during the production of tofu is used as the raw material. First, 15 times the volume of water is added to the weighed dry okara, and the okara solution is formed under sufficient stirring; Add hydrochloric acid to adjust its pH value to 4, and cook for 3 hours in a high-temperature and high-pressure-resistant airtight container at a temperature of 120° C. to form a soybean fiber decomposition liquid.
[0024] Next, cool down the soybean fiber decomposition solution to 100°C within 1 hour, then adjust its pH value to 7.0 with phosphate buffer solution, and continue to keep warm for 2 hours to cause Maillard reaction, so that the ε-amino group of the protein in the raw material Further combined with the reducing carbonyl end of the polysaccharide in the soybean fiber decomposition liquid.
[0025] Then, solid-liquid separation is carried out by means of a plate and frame filter press to obtain a supernatant, and t...
Embodiment 3
[0027] In this example, the dried okara produced as a by-product during the production of isolated soybean protein is used as the raw material. First, 10 times the volume of water is added to the dried okara, and the okara solution is formed under sufficient stirring; then hydrochloric acid is added dropwise to the okara solution. Adjust its pH value to 4.5, and cook at a temperature of 130° C. for 1.5 hours in a high-temperature and high-pressure airtight container to form a soybean fiber decomposition liquid.
[0028] Next, cool down the soybean fiber decomposition solution to 60°C within 1 hour, add phosphate buffer solution dropwise to the decomposition solution to adjust its pH value to 6.0, and continue to keep warm for 5 hours to produce Maillard reaction, so that the protein in the raw material The ε-amino group of the β-amino group is further combined with the reducing carbonyl end of the polysaccharide in the soybean fiber decomposition liquid.
[0029] Then, the sol...
PUM
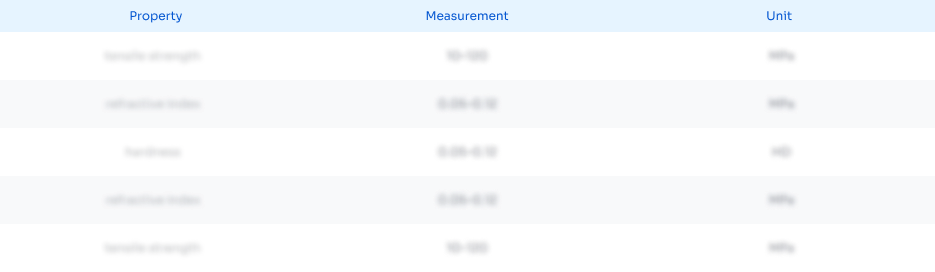
Abstract
Description
Claims
Application Information

- Generate Ideas
- Intellectual Property
- Life Sciences
- Materials
- Tech Scout
- Unparalleled Data Quality
- Higher Quality Content
- 60% Fewer Hallucinations
Browse by: Latest US Patents, China's latest patents, Technical Efficacy Thesaurus, Application Domain, Technology Topic, Popular Technical Reports.
© 2025 PatSnap. All rights reserved.Legal|Privacy policy|Modern Slavery Act Transparency Statement|Sitemap|About US| Contact US: help@patsnap.com