Method for manufacturing photovoltaic connector
A technology of photovoltaic connector and manufacturing method, which is applied in the direction of connection, contact box/base manufacturing, circuit/collector parts, etc., which can solve the problem of limited high temperature resistance of the outer protective layer of the cable, easy damage to the cable, and easy damage to the cable. Cracking and other problems, to achieve good market promotion prospects, flexible production process, outstanding performance characteristics
- Summary
- Abstract
- Description
- Claims
- Application Information
AI Technical Summary
Problems solved by technology
Method used
Examples
Embodiment 1
[0022] The manufacturing method of the photovoltaic connector provided by Embodiment 1 of the present invention comprises the following steps:
[0023] The connector conductor is connected to the cable conductor; the above-mentioned connector conductor and cable conductor are placed in the molding mold 1, polyphenylene ether is melted at a temperature of 180°C and injected into the molding mold 1, and taken out after cooling to complete the connection Layer injection molding to form the connector body;
[0024] Melt the modified polycarbonate at a temperature of 160°C and inject it into the molding mold 2, take it out after cooling to complete the injection molding of the lock head, and form the lock head;
[0025] Place the above-mentioned lock head and connector body in the molding mold 3, melt the modified polyphenylene ether at a temperature of 100°C and pour it into the molding mold 3, take it out after cooling, and complete the injection molding of the sealing layer to f...
Embodiment 2
[0030] The manufacturing method of the photovoltaic connector provided by Embodiment 2 of the present invention includes the following steps:
[0031] The connector conductor is connected to the cable conductor; the above-mentioned connector conductor and cable conductor are placed in the molding mold 1, and the modified polyphenylene ether is melted at a temperature of 250°C and injected into the molding mold 1, and taken out after cooling Complete the injection molding of the connection layer to form the connector body;
[0032] Melt the modified polycarbonate at a temperature of 230°C and inject it into the molding mold 2, take it out after cooling to complete the injection molding of the lock head, and form the lock head;
[0033] Place the above-mentioned lock head and connector body in the molding mold 3, melt the modified polyolefin at a temperature of 150°C and inject it into the molding mold 3, take it out after cooling, and complete the injection molding of the seali...
Embodiment 3
[0038] The manufacturing method of the photovoltaic connector provided by Embodiment 3 of the present invention includes the following steps:
[0039] The connector conductor is connected with the cable conductor; the above-mentioned connector conductor and cable conductor are placed in the molding mold 1, and the modified polyphenylene ether is melted at a temperature of 200°C and injected into the molding mold 1, and taken out after cooling Complete the injection molding of the connection layer to form the connector body;
[0040] Melt the modified polycarbonate at a temperature of 190°C and inject it into the molding mold 2, take it out after cooling to complete the injection molding of the lock head, and form the lock head;
[0041] Place the above-mentioned lock head and connector body in the molding mold 3, melt the modified polyolefin at a temperature of 115°C and inject it into the molding mold 3, and take it out after cooling to complete the injection molding of the s...
PUM
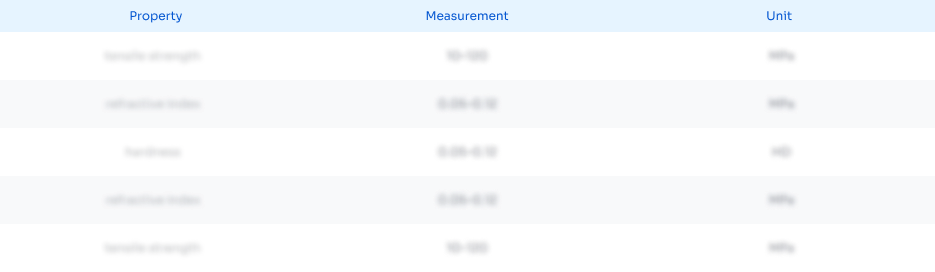
Abstract
Description
Claims
Application Information

- Generate Ideas
- Intellectual Property
- Life Sciences
- Materials
- Tech Scout
- Unparalleled Data Quality
- Higher Quality Content
- 60% Fewer Hallucinations
Browse by: Latest US Patents, China's latest patents, Technical Efficacy Thesaurus, Application Domain, Technology Topic, Popular Technical Reports.
© 2025 PatSnap. All rights reserved.Legal|Privacy policy|Modern Slavery Act Transparency Statement|Sitemap|About US| Contact US: help@patsnap.com