Completely biodegradable food packing material and preparation method thereof
A technology for food packaging and biodegradation, applied in the field of fully biodegradable food packaging materials and their preparation, can solve the problems of affecting packaging quality and effect, reducing mechanical strength, affecting human health, etc. The effect of improving the tensile strength and improving the appearance whiteness
- Summary
- Abstract
- Description
- Claims
- Application Information
AI Technical Summary
Problems solved by technology
Method used
Examples
Embodiment 1
[0020] (1) Configuration of the mixed soaking solution: add 300g sodium hydroxide and 200g thiourea to 3kg of water, cool it to -5°C, then take it out and cool it to room temperature;
[0021] (2) Soak 10 kilograms of 60-70 mesh bamboo fibers in the mixed soaking solution in (1) for 12-24 hours, and then stir the bamboo fiber mixture in a high-speed mixer for 20-30 minutes;
[0022] (3) Take half the amount of potato starch 15 kg, add hot water at 65-75 ℃ and stir for 15-30 minutes until gelatinization;
[0023] (4) Mix the treated bamboo fiber aqueous solution, gelatinized starch, 2.5 kg polycaprolactone, 2 kg ethylene glycol, and 1.0 kg polyacrylic acid (PAA) as a solubilizer, mix and stir for 10-20 minutes, then add talcum powder 1 kg, 1 kg calcium hydroxide, 15 kg remaining ungelatinized starch, stir together for 20-35 minutes;
[0024] (5) Pass the mixed raw materials through a twin-screw extruder, melt, blend, extrude and granulate under the conditions of a temperature ...
Embodiment 2
[0028] (1) Configuration of the mixed soaking solution: add 400g of sodium hydroxide and 350g of thiourea to 5.5kg of water, cool it to -5°C, then take it out and cool it to room temperature;
[0029] (2) Soak 20 kilograms of 60-70 mesh bamboo fibers in the mixed soaking solution in (1) for 12-24 hours, and then stir the bamboo fiber mixture in a high-speed mixer for 20-30 minutes;
[0030] (3) Take 20 kg of half of the potato starch, put it into 2 kg of hot water at 65-75°C and stir for 15-30 minutes to gelatinize;
[0031] (4) Mix the treated bamboo fiber aqueous solution, gelatinized starch, 9 kg of polycaprolactone, 3 kg of ethylene glycol, and 2 kg of polyacrylic acid (PAA) as a solubilizer, mix and stir for 10 to 20 minutes, then add talc powder 1.5 kg, 1.5 kg calcium hydroxide, and the remaining ungelatinized starch, stir together for 20-35 minutes;
[0032] (5) Pass the mixed raw materials through a twin-screw extruder, melt, blend, extrude and granulate under the con...
Embodiment 3
[0036] (1) Configuration of the mixed soaking solution: add 500g of sodium hydroxide and 400g of thiourea to 6kg of water, cool it to -5°C, then take it out and cool it to room temperature;
[0037] (2) Soak 30 kilograms of 60-70 mesh bamboo fibers in the mixed soaking solution in (1) for 12-24 hours, and then stir the bamboo fiber mixture in a high-speed mixer for 20-30 minutes;
[0038] (3) Take 30 kg of half of the potato starch, put it into 5 kg of hot water at 65-75°C and stir for 15-30 minutes to gelatinize;
[0039] (4) Mix the treated bamboo fiber aqueous solution, gelatinized starch, 10 kg of polycaprolactone, 5 kg of ethylene glycol, and 2.5 kg of polyacrylic acid (PAA) as a solubilizer, mix and stir for 10 to 20 minutes, then add talc powder 2 kg, 2 kg of calcium hydroxide, and the remaining ungelatinized starch, stir together for 20-35 minutes;
[0040] (5) Pass the mixed raw materials through a twin-screw extruder, melt, blend, extrude and granulate under the con...
PUM
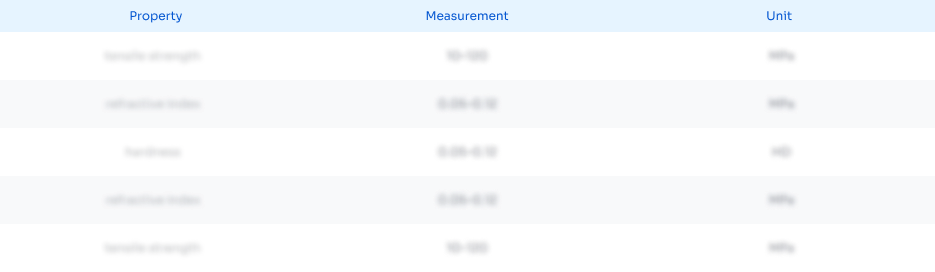
Abstract
Description
Claims
Application Information

- R&D
- Intellectual Property
- Life Sciences
- Materials
- Tech Scout
- Unparalleled Data Quality
- Higher Quality Content
- 60% Fewer Hallucinations
Browse by: Latest US Patents, China's latest patents, Technical Efficacy Thesaurus, Application Domain, Technology Topic, Popular Technical Reports.
© 2025 PatSnap. All rights reserved.Legal|Privacy policy|Modern Slavery Act Transparency Statement|Sitemap|About US| Contact US: help@patsnap.com