Inhibitor addition-based desulfurizing method in iron ore sintering process
A sintering process and iron ore technology, applied in the field of desulfurization, can solve the problems of difficult production process operation, large processing capacity of the water washing system, and decreased desulfurization efficiency, and achieve the effects of low operating cost, simple process flow, and reduced investment costs
- Summary
- Abstract
- Description
- Claims
- Application Information
AI Technical Summary
Problems solved by technology
Method used
Image
Examples
Embodiment Construction
[0016] The present invention will be further described below with reference to the accompanying drawings and embodiments.
[0017] The ammonia-containing compound in the examples adopts urea, and the mass percentage of urea and the sintered material layer is taken as 0.10%, that is, 1 kilogram of urea is used for 1 ton of sintered mixture. During the sintering production process, urea is prepared into a urea solution in the inhibitor aqueous solution proportioning tank 1, and is evenly sprayed on the bottom material layer at the bottom of the material layer of the sintering machine 3 through the inhibitor aqueous solution sprayer 2. During the sintering process, the urea The decomposed ammonia reacts with sulfur oxides to form ammonium sulfate. Before the sintering high temperature arrives, the ammonium sulfate is adsorbed on the dust and taken away by the flue gas. The flue gas from the bellows in the second half of the sintering machine 3 is introduced into ammonium sulfate. ...
PUM
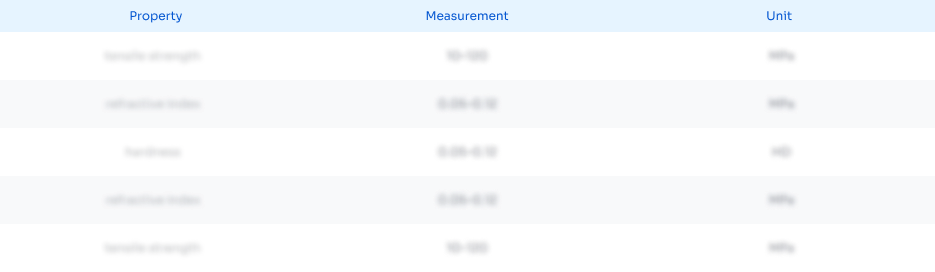
Abstract
Description
Claims
Application Information

- R&D
- Intellectual Property
- Life Sciences
- Materials
- Tech Scout
- Unparalleled Data Quality
- Higher Quality Content
- 60% Fewer Hallucinations
Browse by: Latest US Patents, China's latest patents, Technical Efficacy Thesaurus, Application Domain, Technology Topic, Popular Technical Reports.
© 2025 PatSnap. All rights reserved.Legal|Privacy policy|Modern Slavery Act Transparency Statement|Sitemap|About US| Contact US: help@patsnap.com