All-weather persistent antistatic master batch capable of being subjected to thermoplastic processing and antistatic composite material
An antistatic masterbatch and composite material technology, which is applied in the field of polymer composite material preparation, can solve problems such as single color, high price, and shedding of conductive particles, and achieve simple production process, wide selection range, and long-lasting antistatic performance. Effect
- Summary
- Abstract
- Description
- Claims
- Application Information
AI Technical Summary
Problems solved by technology
Method used
Image
Examples
Embodiment 1
[0038]After stirring 50g polyether type thermoplastic polyurethane, 5g sodium perchlorate, 0.25g antioxidant 168, 1g polyethylene glycol 800 plasticizer and 0.1g oleic acid amide at normal temperature, use a double-roller mill to Knead at 160°C for 6-8 minutes to obtain an antistatic masterbatch sheet, and the obtained masterbatch sheet is cut into pellets by a sample cutter to obtain an antistatic masterbatch. After mixing 40g of ABS and 10g of the above-mentioned masterbatch uniformly at room temperature, the two-roll mill was used to knead again at 160°C for 6-8 minutes to prepare an ABS antistatic composite material sample. The resulting sample was pressurized at 180°C for 5 minutes by a pressure molding machine to obtain a standard sample of ABS antistatic composite material. The surface resistance of the standard sample at 30°C, 55% and 12% relative humidity was 4×10 9 and 2×10 10 ohm / sq.
Embodiment 2
[0040] Plasticize 50g polyether thermoplastic polyurethane, 1g sodium tetrafluoroborate, 1g sodium thiocyanate, 0.25g antioxidant 168, 0.25g antioxidant 1010, 0.25g EDTA-4Na, 1g dibutyl phthalate After mixing the agent and 0.1g of oleic acid amide at room temperature, use a HAAKE internal mixer at 160°C and 30rpm for 8 minutes to make block antistatic masterbatch. After mixing 30g of polypropylene and 20g of the above-mentioned block masterbatch at room temperature, the HAAKE internal mixer was used to banbury again under the same conditions for 6 minutes to obtain a sample block of PP antistatic composite material. The resulting sample block was pressurized at 180°C for 5 minutes by a pressure forming machine to obtain a standard sample of PP antistatic composite material. The surface resistance of the standard sample at 30°C, 55% and 12% relative humidity was 3×10 7 and 1×10 8 ohm / sq.
Embodiment 3
[0042] Stir 5000g polyetheramide copolymer, 125g sodium perchlorate, 125g sodium thiocyanate, 25g antioxidant 168, 100g polyethylene glycol 400 plasticizer, 25g EDTA-4Na and 10g oleic acid amide at room temperature Finally, use a banburying granulator to banbury at 160°C for 6-8 minutes and then cut into pellets to obtain antistatic masterbatch. After mixing 3500g of high-impact polystyrene and 1500g of the above-mentioned masterbatch uniformly at room temperature, a granular durable antistatic HIPS composite material was prepared at 180°C using a twin-screw granulator. After three-layer co-extrusion of the antistatic composite material (inner and outer layers) and HIPS (core layer) at 210°C, a blister sheet for packaging precision electronic components can be obtained. and the surface resistance at 12% relative humidity are 6×10 7 and 4×10 8 ohm / sq.
PUM
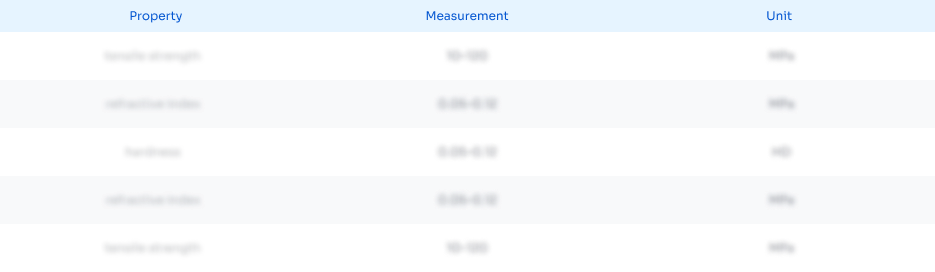
Abstract
Description
Claims
Application Information

- Generate Ideas
- Intellectual Property
- Life Sciences
- Materials
- Tech Scout
- Unparalleled Data Quality
- Higher Quality Content
- 60% Fewer Hallucinations
Browse by: Latest US Patents, China's latest patents, Technical Efficacy Thesaurus, Application Domain, Technology Topic, Popular Technical Reports.
© 2025 PatSnap. All rights reserved.Legal|Privacy policy|Modern Slavery Act Transparency Statement|Sitemap|About US| Contact US: help@patsnap.com