Continuous cutting process for cylinders
A process and process technology, which is applied in the field of tube making and cutting production process, can solve the problems of roll material folding and winding rollers, unable to adjust the transmission speed, uneven bag making line speed, etc., achieve straight cut, shorten cutting time, The effect of taking up little space
- Summary
- Abstract
- Description
- Claims
- Application Information
AI Technical Summary
Problems solved by technology
Method used
Image
Examples
Embodiment Construction
[0018] A continuous tube cutting process, including unwinding, preforming, sewing, cloth storage, measuring range, cutting and conveying processes, figure 1 It is a process flow diagram of the present invention, figure 2 is the equipment diagram used in the present invention, figure 2 Among them, an unwinding machine 1, a cloth holder 2, a hot-melt sewing machine 3, a cloth storage rack 4, a measuring range machine 5, a servo cutting machine 6 and a conveying frame 7 are arranged in sequence. The specific requirements of each process are as follows;
[0019] 1) In the unwinding process, the unwinding frame is a passive double station; there is an active mopping device for constant tension control between the unwinding material and the sewing machine; the unwinding machine is equipped with a protection device to detect the current status of the coil material. When the roll material is used up, the pressure roller is automatically lifted to avoid accidents caused by coil mat...
PUM
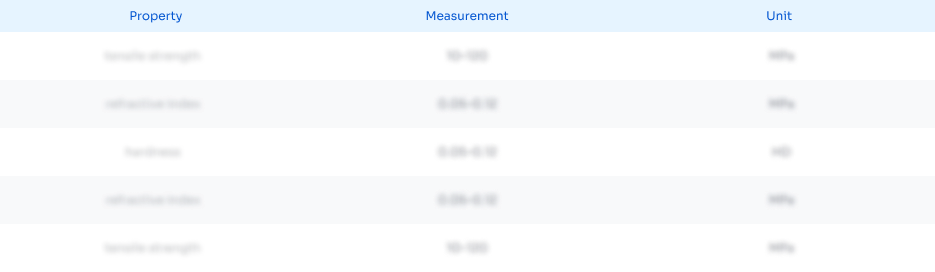
Abstract
Description
Claims
Application Information

- R&D Engineer
- R&D Manager
- IP Professional
- Industry Leading Data Capabilities
- Powerful AI technology
- Patent DNA Extraction
Browse by: Latest US Patents, China's latest patents, Technical Efficacy Thesaurus, Application Domain, Technology Topic, Popular Technical Reports.
© 2024 PatSnap. All rights reserved.Legal|Privacy policy|Modern Slavery Act Transparency Statement|Sitemap|About US| Contact US: help@patsnap.com