Catalyst used for preparing propylene and ethylene by cracking and preparation method thereof
A technology of propylene ethylene and catalyst, which is applied in the field of cracking propylene ethylene catalyst and its preparation. It can solve the problems of poor propylene selectivity, poor thermal stability, and inability to meet long-term operation, and achieve long-term operation and good high-temperature hydrothermal stability. , the effect of not easy to coke and deactivate
- Summary
- Abstract
- Description
- Claims
- Application Information
AI Technical Summary
Problems solved by technology
Method used
Image
Examples
Embodiment 1
[0043] It is 50 grams of HZSM-5 molecular sieves that the silicon-aluminum ratio produced by the commercially available Fudan University Catalyst Production Plant is 60, and 1.44 grams of Na 2 CO 3 Exchange 200ml of the solution, at 60°C, quickly stir and exchange for 1.5-2 hours, then filter the slurry, dry at 120°C for 1.5-2 hours, and after crushing, a modified HZSM-5 molecular sieve a is obtained, in which the sodium content is 0.25 %.
[0044] Examples 2-8 are HZSM-5 molecular sieve modification, the unspecified raw materials, sources and preparation process are the same as in Example 1, and the SiO of the molecular sieve is changed 2 / A1 2 o 3 The molar ratio and alkali metal content were used to obtain the modified ZSM-5 molecular sieve, listed in Table 1.
[0045] Embodiments 9 to 10 are modified HZSM-5 molecular sieves. The unspecified raw materials and preparation process are the same as in Example 1, but 200ml of sodium hydroxide solution containing 1.08 grams i...
Embodiment 11
[0049] 70 grams of the modified HZSM-5 molecular sieve obtained in Example 1 on a dry basis, 60 grams of the SAPO-34 molecular sieve produced by Tianjin Fusheng Dye Factory on a dry basis, and the content produced by Baotou Rare Earth Group Company with a total weight of 0.1% LaO is 36%, CeO 2 The content of 11% rare earth chloride for catalytic cracking is dissolved in JA-25 and SiO produced by Qingdao Ocean Chemical Co., Ltd. containing 70 grams of silica. 2 The content is 25.0% in silica sol, which are mixed together, extruded, dried at 120°C for 2 hours, and calcined at 550°C for 4 hours to obtain the catalyst. Calculated on a dry basis, it contains 35% by weight of modified ZSM-5 molecular sieve and 30% by weight of modified SAPO-34.
[0050] Examples 12-17 adopt the same preparation process as Example 11, modify the SAPO-34 molecular sieve and carrier by changing the rare earth content, and prepare catalysts, which are listed in Table 2. But the binding agent that embo...
Embodiment 18
[0054] exist figure 1 On the shown continuous flow fixed bed reaction device, load 1 ml of the catalyst prepared in Examples 11-17 and ground to 40-60 mesh. Under normal pressure, using carbon-containing four-olefin mixed hydrocarbons as raw materials, the mass space velocity is 2 h -1 , the reaction temperature was 550°C for the reaction, and the product was analyzed by online gas chromatography. Table 3 is the raw material composition of carbon tetraolefins. Table 4 shows the results of the propylene production reaction when the mixed feedstock containing carbon tetraolefins is used as the feed.
[0055] Table 3 Composition of carbon-containing tetraolefin raw materials, m%
[0056] project composition C 2 0.1 C 3 h 6 0.2 C 3 h 8 0.7 i-C 4 h 10 10 n-C 4 h 10 45 n-C 4 h 8 13 i-C 4 h 8 2 t-C 4 h 8 10 c-C 4 h 8 15 ≥C 5 + 3
[0057] Table 4 The reaction results of producin...
PUM
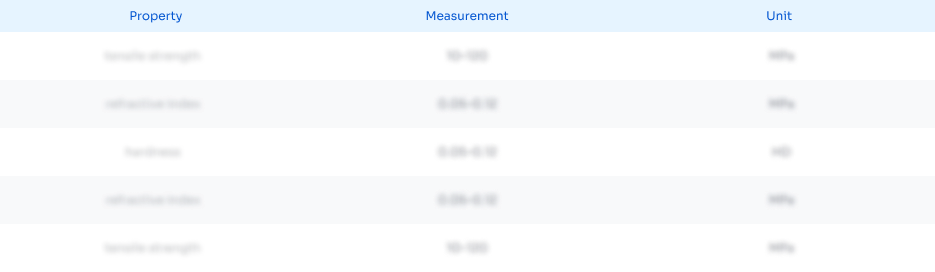
Abstract
Description
Claims
Application Information

- R&D Engineer
- R&D Manager
- IP Professional
- Industry Leading Data Capabilities
- Powerful AI technology
- Patent DNA Extraction
Browse by: Latest US Patents, China's latest patents, Technical Efficacy Thesaurus, Application Domain, Technology Topic, Popular Technical Reports.
© 2024 PatSnap. All rights reserved.Legal|Privacy policy|Modern Slavery Act Transparency Statement|Sitemap|About US| Contact US: help@patsnap.com