Rubber lantern ring produced by micro wave curing process
A microwave vulcanization and rubber technology, applied in the field of rubber products, can solve the problems of low production efficiency of spacer rings and complex production links, and achieve the effects of shortening vulcanization time, weakening the effect of export expansion and improving production efficiency
- Summary
- Abstract
- Description
- Claims
- Application Information
AI Technical Summary
Problems solved by technology
Method used
Image
Examples
Embodiment 1
[0025] To produce a spacer whose size is: inner diameter×outer diameter×length (36±0.5)mm×(46±0.5)mm×(2000±20)mm, the specific steps and process parameters are as follows:
[0026] 1. Extrusion of semi-finished products: the compounded rubber is extruded through the extruder, and the temperature of the extruder is set as follows: the temperature of the head is 60°C, the temperature of the extrusion section is 55°C, the temperature of the plasticizing section is 45°C, and the temperature of the feeding section is The temperature was 45°C.
[0027] 2. Microwave vulcanization: There are 5 microwave sections in the microwave device. The first 2 microwave sections are closed, and the 3 microwave sections are opened. The microwave power of each section is set to 1000W, that is, the total power is 3000W, and the temperature of the microwave section is set to 150°C. . The temperature of the heating section is set to 170°C, 190°C and 210°C respectively from front to back.
[0028] 3 ...
Embodiment 2
[0031] To produce a spacer whose size is: inner diameter × outer diameter × length (15±0.5)mm×(26±0.5)mm×(2000±20)mm, the specific steps and process parameters are as follows:
[0032] 1. Extrusion of semi-finished products: the compounded rubber is extruded through the extruder, and the temperature of the extruder is set as follows: the temperature of the head is 70°C, the temperature of the extrusion section is 65°C, the temperature of the plasticizing section is 40°C, and the temperature of the feeding section is The temperature is 40°C.
[0033] 2. Microwave vulcanization: The microwave device has 6 microwave sections in total, 3 microwave sections before the microwave device is turned off, and 3 microwave sections after it is turned on. The microwave power of each section is set to 1500W, that is, the total power is 4500W, and the temperature of the microwave section is set to 150°C. The temperature of the heating section is set to 180°C, 200°C, and 220°C from front to b...
Embodiment 3
[0037] To produce a spacer whose size is: inner diameter×outer diameter×length (25±0.5)mm×(45±0.5)mm×(2000±20)mm, the specific steps and process parameters are as follows:
[0038] 1. Extrusion of semi-finished products: the compounded rubber is extruded through the extruder, and the temperature of the extruder is set as follows: the temperature of the head is 80°C, the temperature of the extrusion section is 75°C, the temperature of the plasticizing section is 35°C, and the temperature of the feeding section The temperature is 35°C.
[0039] 2. Microwave vulcanization: The microwave device has 5 microwave sections in total, 2 microwave sections before the microwave device is turned off, and 3 microwave sections after it is turned on. The microwave power of each section is set to 2000W, that is, the total power is 6000W, and the temperature of the microwave section is set to 150°C. The temperature of the heating section is set to 190°C, 210°C, and 230°C from front to back.
...
PUM
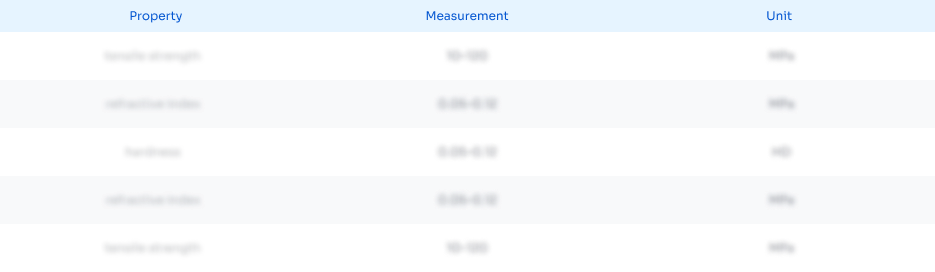
Abstract
Description
Claims
Application Information

- Generate Ideas
- Intellectual Property
- Life Sciences
- Materials
- Tech Scout
- Unparalleled Data Quality
- Higher Quality Content
- 60% Fewer Hallucinations
Browse by: Latest US Patents, China's latest patents, Technical Efficacy Thesaurus, Application Domain, Technology Topic, Popular Technical Reports.
© 2025 PatSnap. All rights reserved.Legal|Privacy policy|Modern Slavery Act Transparency Statement|Sitemap|About US| Contact US: help@patsnap.com