Preparation method for lithium carbonate
A technology of lithium carbonate and lithium bicarbonate, applied in the direction of lithium carbonate;/acid carbonate, etc., can solve the problems of high energy consumption of products, running out of troughs, and inability to recycle the mother liquor, so as to improve the utilization rate and reduce the cost effect
- Summary
- Abstract
- Description
- Claims
- Application Information
AI Technical Summary
Problems solved by technology
Method used
Image
Examples
Embodiment 1
[0027] (1) 5M 3 Add 4100Kg of pure water to the stainless steel dissolution tank, add 825Kg of industrial grade lithium hydroxide under stirring, stir for 30 minutes to dissolve the lithium hydroxide, add 0.78Kg of oxalic acid, add 0.22Kg of barium hydroxide, continue stirring for 10 minutes, use a polypropylene plate Frame filter press filter, collect lithium hydroxide filtrate, stand-by;
[0028] (2) 1.8M 3 Add 1400Kg of pure water in the stainless steel reaction tower, pass into carbon dioxide (pressure is controlled at 0.17Mpa), add industrial grade lithium carbonate 60Kg, then add 0.17Kg oxalic acid, add 0.10Kg barium hydroxide, continue to pass into carbon dioxide to solution pH=8, Use a polypropylene plate and frame filter press to collect the lithium bicarbonate filtrate for use;
[0029] (3)5M 3 Add the lithium bicarbonate solution 3640Kg of step (2) and the lithium hydroxide solution 1050Kg of step (1) in the stainless steel reaction tank, stir, be heated to 60 ℃,...
Embodiment 2
[0035] (1) 5M 3 Add 4200Kg of pure water to the stainless steel dissolution tank, add 845Kg of industrial grade lithium hydroxide under stirring, stir for 30 minutes to dissolve lithium hydroxide, add 0.94Kg of oxalic acid, add 0.43Kg of barium hydroxide, continue stirring for 10 minutes, and use a polypropylene plate Frame filter press filter, collect lithium hydroxide filtrate, stand-by;
[0036] (2) 1.8M 3Add 1400Kg of pure water in the stainless steel reaction tower, pass into carbon dioxide (pressure is controlled at 0.2Mpa), add industrial grade lithium carbonate 60Kg, then add 0.11Kg oxalic acid, add 0.14Kg barium hydroxide, continue to pass into carbon dioxide to solution pH=8.5, Use a polypropylene plate and frame filter press to collect the lithium bicarbonate filtrate for use;
[0037] (3)5M 3 Add the lithium bicarbonate solution 3640Kg of step (2) and the lithium hydroxide solution 1050Kg of step (1) in the stainless steel reaction tank, stir, be heated to 65 ℃,...
PUM
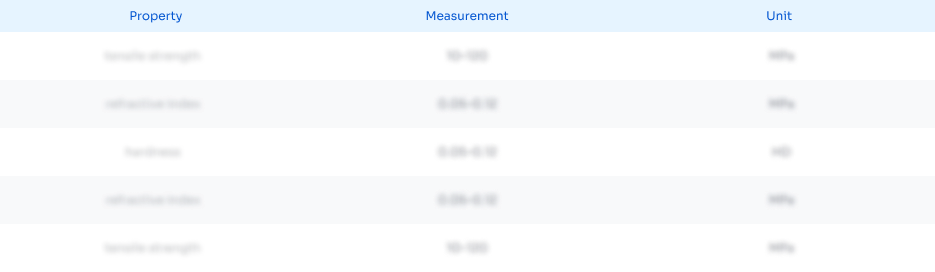
Abstract
Description
Claims
Application Information

- R&D Engineer
- R&D Manager
- IP Professional
- Industry Leading Data Capabilities
- Powerful AI technology
- Patent DNA Extraction
Browse by: Latest US Patents, China's latest patents, Technical Efficacy Thesaurus, Application Domain, Technology Topic, Popular Technical Reports.
© 2024 PatSnap. All rights reserved.Legal|Privacy policy|Modern Slavery Act Transparency Statement|Sitemap|About US| Contact US: help@patsnap.com