Manufacture method and manufacture device of lapping isolated installation wire
A technology of wrapping insulation and manufacturing methods, applied in the direction of conductor/cable insulation, etc., can solve the problems of loss of manufacturers and users, black spots on the surface of wires, and affecting the quality of wires, so as to save manpower and material resources and improve the quality of black spots Problem control, technical effect outstanding effect
- Summary
- Abstract
- Description
- Claims
- Application Information
AI Technical Summary
Problems solved by technology
Method used
Image
Examples
Embodiment 1
[0020] (Example 1, manufacturing method of wrapping insulated installation wire)
[0021] This embodiment is a manufacturing method of a polytetrafluoroethylene film wrapping installation line, comprising the following steps:
[0022] ①Slitting the plastic film 10 according to the preset width, and then winding the slit plastic film 10 for standby use, and blowing ion wind to the plastic film 10 during slitting and winding;
[0023] ②Let the silver-plated copper wire 9 pass through the alcohol tank 1 to clean the outer surface of the wire 9, and then make the wire 9 enter the antistatic device 2; the antistatic device 2 is provided with a plastic film frame 3 and a coating machine 4 ;
[0024] ③In the antistatic device 2, wrap the plastic film 10 after slitting on the outer circumference of the wire 9 with a wrapping machine 4, thereby obtaining a blank;
[0025] ④ Send the billet directly from the outlet of the coating machine 4 to the high-temperature sintering device 5, a...
Embodiment 2
[0032] (Example 2, manufacturing device of wrapping insulated installation wire)
[0033] figure 1 It is a structural schematic diagram of a manufacturing device for wrapping insulated installation wires in the present invention, showing a specific embodiment of the present invention.
[0034] This embodiment is a manufacturing device for wrapping insulated installation wires with polytetrafluoroethylene film, including a coating machine 4 for wrapping the plastic film 10 on the wire 9, and a coating machine 4 for sintering the plastic film 10 on the wire 9 high-temperature sintering device 5, an alcohol pool 1 for cleaning wires 9, an antistatic device 2 for preventing dust in the air from adhering to the plastic film 10, and an auxiliary antistatic device for preventing dust in the air from adhering to the blank Dust device6.
[0035] The alcohol pool 1, coating machine 4, high temperature sintering device 5 and antistatic device 2 are integrally arranged on the frame hous...
PUM
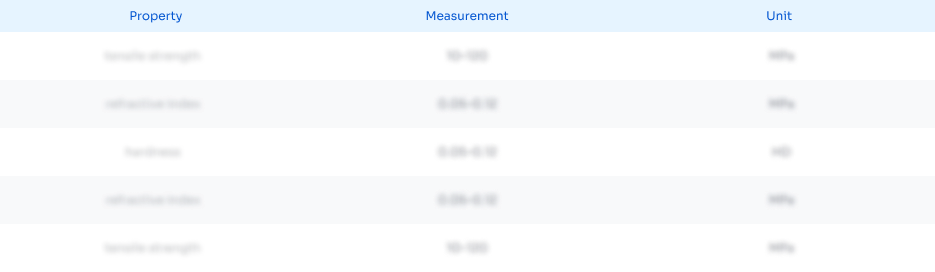
Abstract
Description
Claims
Application Information

- R&D Engineer
- R&D Manager
- IP Professional
- Industry Leading Data Capabilities
- Powerful AI technology
- Patent DNA Extraction
Browse by: Latest US Patents, China's latest patents, Technical Efficacy Thesaurus, Application Domain, Technology Topic, Popular Technical Reports.
© 2024 PatSnap. All rights reserved.Legal|Privacy policy|Modern Slavery Act Transparency Statement|Sitemap|About US| Contact US: help@patsnap.com