Connecting rod of engine and making method thereof
A technology for connecting rods and connecting rods of engines, which is applied in the direction of connecting rods, connecting rod bearings, mechanical equipment, etc. It can solve the problems of many influencing factors and difficult control of cracking processing quality, and achieve the effect of large selectivity and easy tooth root strength
- Summary
- Abstract
- Description
- Claims
- Application Information
AI Technical Summary
Problems solved by technology
Method used
Image
Examples
Embodiment 2
[0042] Such as Figure 6 , 7 As shown, an engine connecting rod includes a connecting rod body 1 and a connecting rod cover 2. The first mating surface 1a of the connecting rod body 1 is formed with a first groove group and a first groove group vertically intersecting with the first groove group. A convex tooth group, the first groove group includes two first grooves 3 arranged parallel to each other, the first convex tooth group includes two first convex teeth 4 arranged parallel to each other and shaped as a rectangle, the connecting rod cover 2 On the second mating surface 2a of the first groove group, a second convex tooth group consisting of rectangular second convex teeth 5 and a second concave tooth group matching with the first convex tooth group are formed. The second groove group composed of 6.
[0043] A method of producing the above-mentioned engine connecting rod, comprising the following steps: referring to Figure 8 , first take the initial connecting rod tha...
Embodiment 3
[0047] Such as Figure 11 , 12 As shown, a connecting rod for an engine includes a connecting rod body 1 and a connecting rod cover 2. The first mating surface 1a of the connecting rod body 1 is formed with a first groove group and a first groove group intersecting with the first groove group. Convex tooth group, the first groove group includes a first groove 3, the first convex tooth group includes a trapezoidal first convex tooth 4, the angle between the first groove 3 and the first convex tooth 4 is 60°, the second mating surface 2a of the connecting rod cover 2 is formed with a second convex tooth group consisting of a trapezoidal second convex tooth 5 that fits with the first groove group, and a second convex tooth group that is compatible with the first convex tooth group. The matched second groove group is composed of the second groove 6 .
PUM
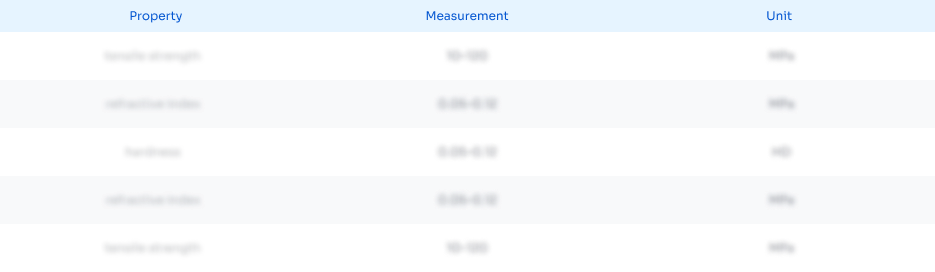
Abstract
Description
Claims
Application Information

- Generate Ideas
- Intellectual Property
- Life Sciences
- Materials
- Tech Scout
- Unparalleled Data Quality
- Higher Quality Content
- 60% Fewer Hallucinations
Browse by: Latest US Patents, China's latest patents, Technical Efficacy Thesaurus, Application Domain, Technology Topic, Popular Technical Reports.
© 2025 PatSnap. All rights reserved.Legal|Privacy policy|Modern Slavery Act Transparency Statement|Sitemap|About US| Contact US: help@patsnap.com