TDOF (Three Degrees of Freedom) passive ball joint with attitude detection and applicable to ball motor
A technology of ball joints and degrees of freedom, applied in manipulators, manufacturing tools, joints, etc., can solve problems such as loss, high energy, and joint kinematics singularity, and achieve the effect of reducing excessive friction and low friction
- Summary
- Abstract
- Description
- Claims
- Application Information
AI Technical Summary
Problems solved by technology
Method used
Image
Examples
Embodiment Construction
[0048] The present invention will be further described in detail below in conjunction with the accompanying drawings.
[0049] A ball motor of the present invention includes a passive ball joint assembly 1, a ball motor stator assembly 2, a ball motor rotor assembly 3 and a base 4; a passive ball with three degrees of freedom for attitude detection designed in the present invention is installed The ball motor of joint 1, which can realize continuous rotation with three degrees of freedom in space. The passive ball joint assembly 1 is installed on the positioning inner ring 402 of the base 4, the bottom of the stator 2B of the ball motor stator assembly 2 is installed on the four L-shaped connectors of the positioning inner ring 402 of the base 4, and the ball motor rotor assembly 3 is installed on the passive ball joint assembly 1.
[0050] 1. Base 4
[0051] see Figure 1A As shown, the positioning outer ring 401 of the base 4 is provided with an A threaded hole 404, and t...
PUM
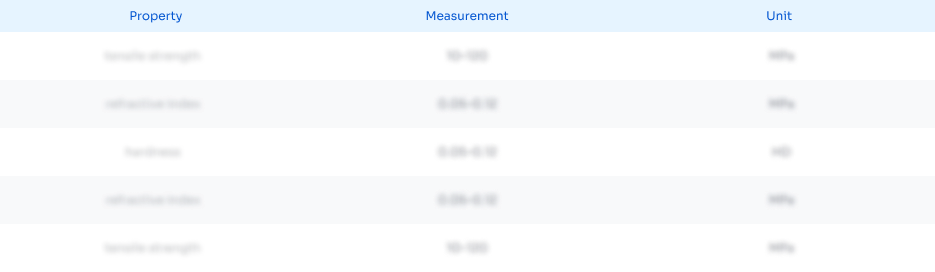
Abstract
Description
Claims
Application Information

- R&D Engineer
- R&D Manager
- IP Professional
- Industry Leading Data Capabilities
- Powerful AI technology
- Patent DNA Extraction
Browse by: Latest US Patents, China's latest patents, Technical Efficacy Thesaurus, Application Domain, Technology Topic, Popular Technical Reports.
© 2024 PatSnap. All rights reserved.Legal|Privacy policy|Modern Slavery Act Transparency Statement|Sitemap|About US| Contact US: help@patsnap.com