Liquid crystal panel and manufacturing method thereof
A liquid crystal panel and display substrate technology, applied in nonlinear optics, instruments, optics, etc., to achieve the effect of increasing vertical distance and reducing parasitic capacitance
- Summary
- Abstract
- Description
- Claims
- Application Information
AI Technical Summary
Problems solved by technology
Method used
Image
Examples
Embodiment 1
[0066] image 3 It is a partial top view structural schematic diagram of the first display substrate in the liquid crystal panel provided by Embodiment 1 of the present invention, Figure 4 It is a partial top view structural schematic diagram of the second display substrate in the liquid crystal panel provided by Embodiment 1 of the present invention, Figure 5 It is a schematic diagram of a partial side-view cross-sectional structure of a liquid crystal panel provided in Embodiment 1 of the present invention, Figure 5 for along image 3 The B-B line in and Figure 4 Obtained by sectioning the C-C line in . The liquid crystal panel of this embodiment includes a first display substrate 100 and a second display substrate 200 arranged opposite to each other, and a liquid crystal 300 is filled between the first display substrate 100 and the second display substrate 200 .
[0067] The first display substrate 100 specifically includes a first base substrate 1 , on which a plur...
Embodiment 2
[0074] Figure 6 It is a partial top view structural schematic diagram of the first display substrate in the liquid crystal panel provided by Embodiment 2 of the present invention, Figure 7 It is a partial top view structural schematic diagram of the second display substrate in the liquid crystal panel provided by Embodiment 2 of the present invention, Figure 8 It is a schematic diagram of a partial side-view cross-sectional structure of a liquid crystal panel provided in Embodiment 2 of the present invention, Figure 8 for along Figure 6 The D-D line in and Figure 7 Obtained by sectioning the E-E line in . The difference between this embodiment and Embodiment 1 is that the common electrode lines 5 are formed on the second base substrate 14, and the common electrode lines 5 are covered with a common electrode insulating layer 23, and the pixel electrodes 4 and the common electrodes 6 are formed on the common electrode lines. On the insulating layer 23 , a third via hol...
Embodiment 3
[0077] Figure 9 It is a partial top view structural schematic diagram of the second display substrate in the liquid crystal panel provided by Embodiment 3 of the present invention, Figure 10 It is a schematic diagram of a partial side-view cross-sectional structure of a liquid crystal panel provided in Embodiment 3 of the present invention, Figure 10 for along Figure 9 The F-F line in the section is obtained, and Figure 10 3 shows the first display substrate 100 and the liquid crystal 300 . The difference between this embodiment and the above-mentioned second embodiment is that the second embodiment is an IPS mode LCD in which the pixel electrode 4 and the common electrode 6 are formed on the same layer. interval, and the pixel electrode 4 has a comb pattern with multiple slits, and the common electrode 6 is an FFS mode LCD with a block pattern corresponding to the pixel unit area.
[0078] In this embodiment, the structure of the first display substrate 100 can refer...
PUM
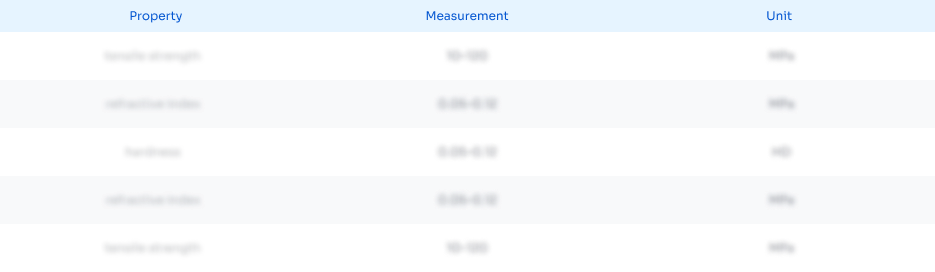
Abstract
Description
Claims
Application Information

- Generate Ideas
- Intellectual Property
- Life Sciences
- Materials
- Tech Scout
- Unparalleled Data Quality
- Higher Quality Content
- 60% Fewer Hallucinations
Browse by: Latest US Patents, China's latest patents, Technical Efficacy Thesaurus, Application Domain, Technology Topic, Popular Technical Reports.
© 2025 PatSnap. All rights reserved.Legal|Privacy policy|Modern Slavery Act Transparency Statement|Sitemap|About US| Contact US: help@patsnap.com