Preparation method of catalyst component for olefin polymerization and catalyst
A technology for olefin polymerization and catalysts, which is applied in the preparation of catalyst components for olefin polymerization and the field of catalysts. It can solve the problems of difficult control of catalyst particle shape, many fine polymer powders, and difficult adjustment of particle size.
- Summary
- Abstract
- Description
- Claims
- Application Information
AI Technical Summary
Problems solved by technology
Method used
Image
Examples
Embodiment 1
[0051] In the reaction kettle that has been repeatedly replaced by high-purity nitrogen, add 0.05 moles of anhydrous magnesium chloride, 0.75 moles of toluene, 0.1 moles of epichlorohydrin, and 0.033 moles of tributyl phosphate in sequence. , reacted for 1.5 hours, then added 1.9 mmoles of dibutyl phthalate, reacted for 1.0 hours, cooled to -28°C, added dropwise 0.51 moles of titanium tetrachloride, and then added 1.4 mmoles of 3,5 diluted with 0.1 moles of toluene Heptanediol dibenzoate and 4.4 mmol of diphenyldimethoxysilane continued to react for one hour, and the temperature was gradually raised to 85° C., during which solid particles were precipitated. Add 2.6 millimoles of dibutyl phthalate to 85°C, keep the temperature for one hour, filter off the mother liquor, wash and filter the liquid with inert diluent toluene several times, add 0.44 moles of titanium tetrachloride, 0.7 moles of toluene at 110°C Keep the temperature for 2 hours, filter and repeat the treatment twic...
Embodiment 2
[0053] In the reaction kettle that has been repeatedly replaced by high-purity nitrogen, add 0.05 moles of anhydrous magnesium chloride, 0.75 moles of toluene, 0.1 moles of epichlorohydrin, and 0.033 moles of tributyl phosphate in sequence. , reacted for 1.5 hours, then added 3.9 mmoles of dibutyl phthalate, reacted for 1.0 hours, cooled to -28°C, added dropwise 0.51 moles of titanium tetrachloride, and then added 1.4 mmoles of 3,5 diluted with 0.1 moles of toluene Heptanediol dibenzoate and 4.4 mmol of diphenyldimethoxysilane continued to react for one hour, and the temperature was gradually raised to 85° C., during which solid particles were precipitated. Keep the temperature at 85°C for one hour, filter the mother liquor, wash and filter the liquid with inert diluent toluene several times, add 0.44 moles of titanium tetrachloride and 0.7 moles of toluene, keep the temperature at 110°C for 1 hour, and repeat the treatment twice after filtration. Then, it was washed with hexa...
Embodiment 3
[0055] Same as in Example 1, only changing 4.4 mmoles of diphenyldimethoxysilane to 6.6 mmoles of diphenyldimethoxysilane.
PUM
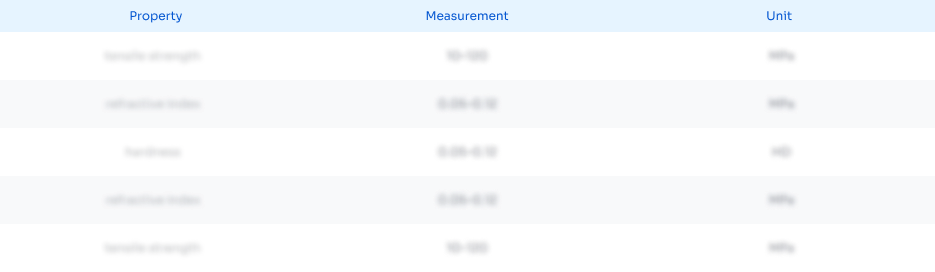
Abstract
Description
Claims
Application Information

- R&D
- Intellectual Property
- Life Sciences
- Materials
- Tech Scout
- Unparalleled Data Quality
- Higher Quality Content
- 60% Fewer Hallucinations
Browse by: Latest US Patents, China's latest patents, Technical Efficacy Thesaurus, Application Domain, Technology Topic, Popular Technical Reports.
© 2025 PatSnap. All rights reserved.Legal|Privacy policy|Modern Slavery Act Transparency Statement|Sitemap|About US| Contact US: help@patsnap.com