Bender transducer for generating electrical energy from mechanical deformations
A mechanical deformation, transducer technology, applied in the direction of generator/motor, piezoelectric device/electrostrictive device, piezoelectric/electrostrictive/magnetostrictive device, etc., to improve stability, improve reliability, The effect of simple and reliable contact
- Summary
- Abstract
- Description
- Claims
- Application Information
AI Technical Summary
Problems solved by technology
Method used
Image
Examples
Embodiment Construction
[0026] one in figure 1 The bending transducer 1a shown in includes a deformable carrier 2a and a piezoelectric element 3a. The carrier 2a has a planar and plane-parallel shape and is elastically deformable; here, the carrier is supported or clamped on the support elements 13a with its two opposite side regions 14, so that Deformation between, especially bending deformation. The first connecting electrode 4 a and the second connecting electrode 5 a are applied as part of a structured, electrically conductive layer, in particular a metal layer, on the upper side 16 a of the carrier 2 a by means of a photolithographic process or an etching process, and along the lateral, side Extend outward in the direction.
[0027] The piezo element 3 a is also planar; it is made in particular of a ceramic material and has a consistent polarity direction P1 in this embodiment. The piezoelectric element has a first lower electrode 17a on its lower side serving as a connection side and a first...
PUM
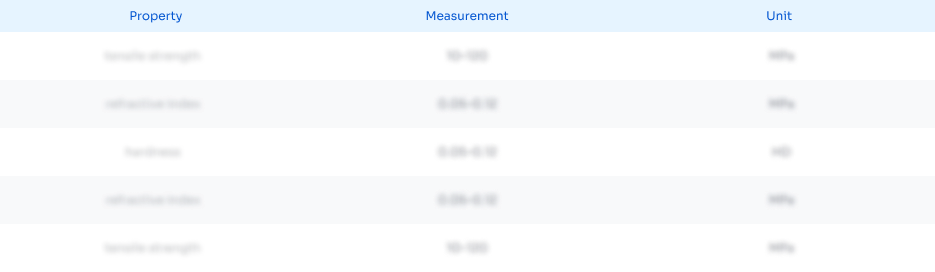
Abstract
Description
Claims
Application Information

- R&D
- Intellectual Property
- Life Sciences
- Materials
- Tech Scout
- Unparalleled Data Quality
- Higher Quality Content
- 60% Fewer Hallucinations
Browse by: Latest US Patents, China's latest patents, Technical Efficacy Thesaurus, Application Domain, Technology Topic, Popular Technical Reports.
© 2025 PatSnap. All rights reserved.Legal|Privacy policy|Modern Slavery Act Transparency Statement|Sitemap|About US| Contact US: help@patsnap.com