Truck volumetric measurement method based on laser triangulation
A technology of laser triangulation and volume measurement, which is applied in the direction of measuring devices, optical devices, instruments, etc., can solve the problems of lower reliability, lower precision, and slow scanning speed, etc., and achieve good practical results
- Summary
- Abstract
- Description
- Claims
- Application Information
AI Technical Summary
Problems solved by technology
Method used
Image
Examples
Embodiment 1
[0039] Step 1. Obtain the length L of the vehicle under test. The specific operation is:
[0040] Step 1: Set three measurement points A, B, and C sequentially along the vehicle driving direction in the green channel of the expressway; the distance between the first measurement point A and the second measurement point B is S 1 is 9.96 meters; the distance between the first measuring point and the third measuring point is S 2 It is 17.06 meters. Install a photoelectric trigger for sensing the arrival and departure of the measured vehicle on the three measurement points A, B, and C respectively; install an axle detection to obtain the number of axles of the measured vehicle 10 meters before the first measurement point A Device 13;
[0041] Step 2: when the vehicle under test 11 passes the axle detector 13, the device acquires the axle number n=4 of the vehicle under test;
[0042] Step 3: When the front part of the vehicle under test 11 reaches the first measurement point A, ...
Embodiment 2
[0057] Step 1. Obtain the length L of the vehicle under test. The specific operation is:
[0058] Step 1: Set three measurement points A, B, and C sequentially along the vehicle driving direction in the green channel of the expressway; the distance between the first measurement point A and the second measurement point B is S 1 is 9.96 meters; the distance between the first measuring point and the third measuring point is S 2 It is 17.06 meters. Install a photoelectric trigger for sensing the arrival and departure of the measured vehicle on the three measurement points A, B, and C respectively; install an axle detection to obtain the number of axles of the measured vehicle 10 meters before the first measurement point A Device 13;
[0059] Step 2: when the vehicle under test 11 passes the axle detector 13, the device acquires the number of axles n=6 of the vehicle under test 11;
[0060] Step 3: When the front part of the vehicle under test 11 reaches the first measurement po...
PUM
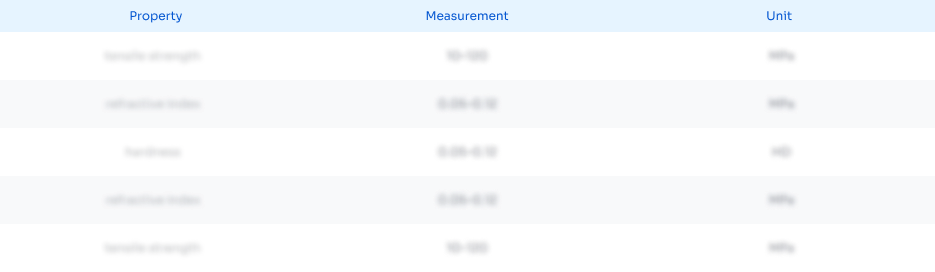
Abstract
Description
Claims
Application Information

- R&D Engineer
- R&D Manager
- IP Professional
- Industry Leading Data Capabilities
- Powerful AI technology
- Patent DNA Extraction
Browse by: Latest US Patents, China's latest patents, Technical Efficacy Thesaurus, Application Domain, Technology Topic, Popular Technical Reports.
© 2024 PatSnap. All rights reserved.Legal|Privacy policy|Modern Slavery Act Transparency Statement|Sitemap|About US| Contact US: help@patsnap.com