Calcium magnesium zinc composite thermal stabilizer, preparation method and application thereof
A composite heat stabilizer, heat stabilizer technology, applied in
The present invention belongs to PVC field, can solve the problems such as poor transparency, poor stability, easy frosting, reaches the effect of excellent weather resistance
- Summary
- Abstract
- Description
- Claims
- Application Information
AI Technical Summary
Problems solved by technology
Method used
Examples
Embodiment 1
[0026] 1. Preparation of calcium intermediates
[0027] In the reaction tank, put 100 parts of aliphatic carboxylic acid, 45 parts of aromatic carboxylic acid and 50 parts of oleic acid, and start stirring at a constant speed. Inject steam into the jacket of the reaction tank to heat the material, control the amount of steam in the jacket, slowly add 30 parts of aromatic carboxylic acid when the temperature of the material rises to 70°C-80°C, stir for 10 minutes to fully dissolve, Increase the temperature to 90°C and add 250 parts of Ca(OH) 2 , when Ca(OH) 2 When everything is put into the reaction tank, the temperature is kept at 100°C, the feeding port is locked, and a certain amount of nitrogen is introduced from the top of the reaction tank to completely discharge the steam in the reaction tank, so that the material can react without contact with the air at all, and the temperature rises , at the same time, in the reaction process, the water generated by the reaction of ...
Embodiment 2
[0035] 1. Preparation of calcium intermediates
[0036] In the reaction tank, put 120 parts of aliphatic carboxylic acid, 75 parts of aromatic carboxylic acid and 75 parts of oleic acid, and start stirring at a constant speed. Inject steam into the jacket of the reaction tank to heat the material, control the amount of steam in the jacket, slowly add 15 parts of aromatic carboxylic acid when the temperature of the material rises to 70°C-80°C, stir for 10 minutes to fully dissolve, Increase the temperature to 90°C and add 275 parts of Ca(OH) 2 . When Ca(OH) 2When everything is put into the reaction tank, the temperature is kept at 100°C, the feeding port is locked, and a certain amount of nitrogen is introduced from the top of the reaction tank to completely discharge the chamber steam in the reaction tank, so that the material can be reacted without contact with the air at all. Heating up, at the same time, during the reaction process, the water generated by the reaction of...
Embodiment 3
[0044] 1. Preparation of calcium intermediates
[0045] In the reaction tank, put 110 parts of aliphatic carboxylic acid, 65 parts of aromatic carboxylic acid and 55 parts of oleic acid, and start stirring at a constant speed. Inject steam into the jacket of the reaction tank to heat the material, control the amount of steam in the jacket, slowly add 15 parts of aromatic carboxylic acid when the temperature of the material rises to 70°C-80°C, stir for 10 minutes to fully dissolve, Increase the temperature to 90°C and add 250 parts of Ca(OH) 2 . When Ca(OH) 2 When everything is put into the reaction tank, the temperature is kept at 100°C, the feeding port is locked, and a certain amount of nitrogen is introduced from the top of the reaction tank to completely discharge the chamber steam in the reaction tank, so that the material can be reacted without contact with the air at all. Heating up, at the same time, during the reaction process, the water generated by the reaction o...
PUM
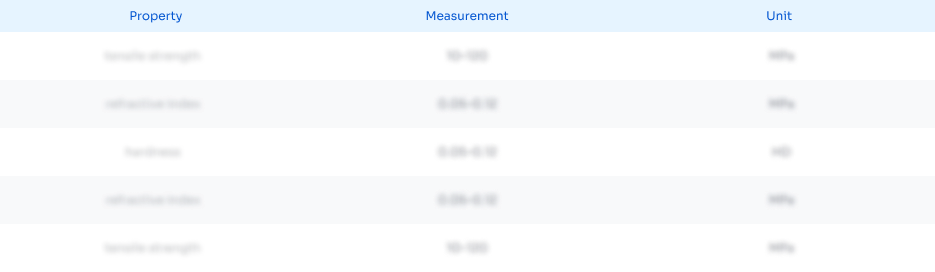
Abstract
Description
Claims
Application Information

- Generate Ideas
- Intellectual Property
- Life Sciences
- Materials
- Tech Scout
- Unparalleled Data Quality
- Higher Quality Content
- 60% Fewer Hallucinations
Browse by: Latest US Patents, China's latest patents, Technical Efficacy Thesaurus, Application Domain, Technology Topic, Popular Technical Reports.
© 2025 PatSnap. All rights reserved.Legal|Privacy policy|Modern Slavery Act Transparency Statement|Sitemap|About US| Contact US: help@patsnap.com