Method for adsorption deacidification of diesel oil and production of bentonite naphthenate
A technology of naphthenic acid and bentonite, applied in chemical instruments and methods, refined hydrocarbon oil, petroleum industry, etc., can solve the problems of high price and high production cost, and achieve the effect of reducing adsorption cost and avoiding pollution
- Summary
- Abstract
- Description
- Claims
- Application Information
AI Technical Summary
Problems solved by technology
Method used
Examples
Embodiment 1
[0015] Add 1 part of calcium hydroxide-loaded clay with a particle size of 100 mesh and a calcium hydroxide content of 8 mmol / g to the first deacidification diesel, and deacidify at 55°C for 100 minutes while stirring to obtain a deacidification diesel suspension; Filtrate the deacidified diesel suspension to obtain finished diesel oil with an acid value of 2mgKOH / 100mL and a filter cake; add the filter cake to 150 parts of calcium hydroxide-loaded clay in raw diesel oil with an acid value of 40mgKOH / 100mL, and stir at 60°C Deacidification under 90 minutes to obtain the first deacidification diesel suspension; the first deacidification diesel suspension is filtered to obtain the first deacidification diesel and naphthenic acid bentonite filter cake, and the first deacidification diesel is returned to step 1 to carry out The second deacidification: the naphthenic acid bentonite filter cake is recovered with steam to recover residual diesel oil, dried and pulverized to obtain nap...
Embodiment 2
[0017] Add 1 part of calcium hydroxide-loaded clay with a particle size of 100 mesh and a calcium hydroxide content of 6 mmol / g to the first deacidified diesel oil, and deacidify at 60°C for 60 minutes under stirring to obtain a suspension of deacidified diesel oil; Filtrate the deacidified diesel suspension to obtain finished diesel oil and filter cake with an acid value of 1.8 mgKOH / 100 mL; add the filter cake to raw diesel oil with an acid value of 30 mgKOH / 100 mL of 200 parts of calcium hydroxide-loaded clay at 65 °C Deacidify under stirring for 50 minutes to obtain the first deacidified diesel suspension; filter the first deacidified diesel suspension to obtain the first deacidified diesel and naphthenic acid bentonite filter cake, and return to step 1 for the first deacidified diesel The second deacidification is carried out; the naphthenic acid bentonite filter cake is recovered with steam to recover residual diesel oil, dried and pulverized to obtain naphthenic acid ben...
Embodiment 3
[0019] Add 1 part of calcium hydroxide-loaded clay with a particle size of 200 mesh and a calcium hydroxide content of 10 mmol / g to the first deacidified diesel oil, and deacidify at 50°C for 70 minutes under stirring to obtain a suspension of deacidified diesel oil; Filtrate the sour diesel suspension to obtain finished diesel oil and filter cake with an acid value of 2mgKOH / 100mL; add the filter cake to 250 parts of calcium hydroxide loaded clay in raw diesel oil with an acid value of 25mgKOH / 100mL, and stir at 55°C Deacidification for 60 minutes to obtain the first deacidification diesel suspension; the first deacidification diesel suspension is filtered to obtain the first deacidification diesel and naphthenic acid bentonite filter cake, and the first deacidification diesel returns to step 1 for the first deacidification. Secondary deacidification; the naphthenic acid bentonite filter cake is recovered with steam to recover residual diesel oil, dried and crushed to obtain n...
PUM
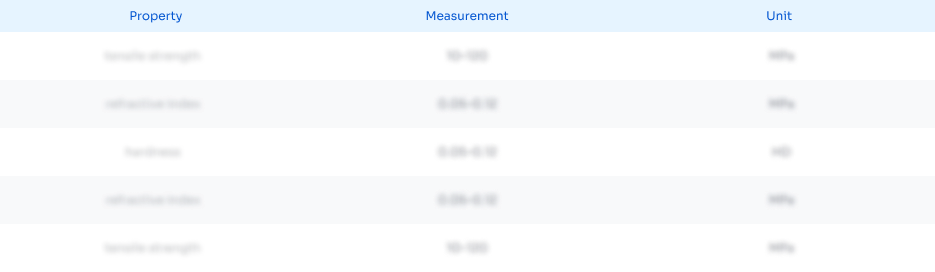
Abstract
Description
Claims
Application Information

- R&D
- Intellectual Property
- Life Sciences
- Materials
- Tech Scout
- Unparalleled Data Quality
- Higher Quality Content
- 60% Fewer Hallucinations
Browse by: Latest US Patents, China's latest patents, Technical Efficacy Thesaurus, Application Domain, Technology Topic, Popular Technical Reports.
© 2025 PatSnap. All rights reserved.Legal|Privacy policy|Modern Slavery Act Transparency Statement|Sitemap|About US| Contact US: help@patsnap.com