Extraction technology of alumina and potassium sulfate from alunite by using hot-pressing leaching process
- Summary
- Abstract
- Description
- Claims
- Application Information
AI Technical Summary
Problems solved by technology
Method used
Image
Examples
Embodiment 1
[0027] The present embodiment proposes a method for producing alumina and potassium sulfate by treating alunite with a hot-pressing leaching process with low production cost, short technological process, environmental friendliness, and easy industrial implementation. The method overcomes the disadvantages of high roasting energy consumption, complex process flow, difficult operation, serious environmental pollution and the like in the prior art of alumite treatment.
[0028] In this example, the alunite was leached by hot pressing with potassium hydroxide solution. The leaching slurry is filtered and separated to precipitate aluminum hydroxide with sulfuric acid, the aluminum hydroxide separated by filtration is calcined to obtain finished alumina, and the mother liquor is evaporated, concentrated and crystallized to obtain finished potassium sulfate. It includes the following steps:
[0029] The first step: add alunite and potassium hydroxide solution into the slurry mixing ...
Embodiment 2
[0044] Take 96.4 g of alunite and 5% potassium hydroxide solution to carry out hot pressing leaching under the conditions of liquid-solid ratio of 3, temperature of 140 ° C, and time of 45 min, and filtration to achieve solid-liquid separation to obtain aluminum-containing potassium mother liquor. The dissolution rates of alumina and potassium oxide in this process were 78.25% and 90.69%, respectively.
[0045] After the mother liquor containing aluminum and potassium is desiliconized, the desiliconized semen with a silicon content index greater than 300 is obtained, and sulfuric acid is added to precipitate aluminum hydroxide (the amount of sulfuric acid added is to prevent the precipitated aluminum hydroxide from returning to dissolve), and 1.5 times the volume of the filtrate is heated. The aluminum hydroxide obtained by washing with water, filtering and drying was calcined at 1100°C to obtain primary alumina. The lotion is sent to the hot pressing system for recycling.
...
Embodiment 3
[0048] Take 130 g of alunite and 7% potassium hydroxide solution to carry out hot-press leaching under the conditions of liquid-solid ratio of 3, temperature of 150 ° C, and time of 1 h, and filtration to achieve solid-liquid separation to obtain aluminum-containing potassium mother liquor.
[0049] The mother liquor containing aluminum and potassium is subjected to desiliconization, acid precipitation of aluminum hydroxide and crystallization of precipitation aluminum mother liquor according to the conditions of Example 1 to obtain potassium sulfate product after evaporation, concentration and crystallization. The technical indicators are shown in Table 1 below.
PUM
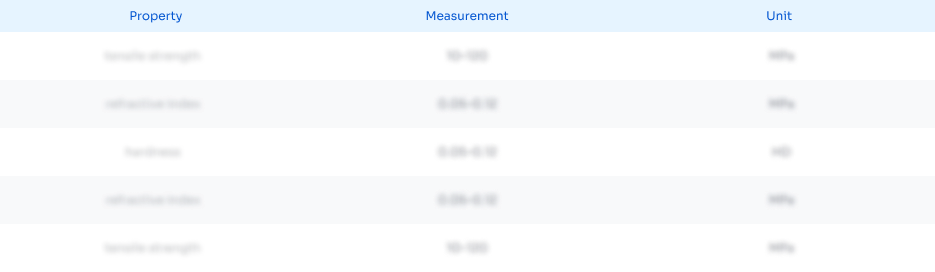
Abstract
Description
Claims
Application Information

- R&D
- Intellectual Property
- Life Sciences
- Materials
- Tech Scout
- Unparalleled Data Quality
- Higher Quality Content
- 60% Fewer Hallucinations
Browse by: Latest US Patents, China's latest patents, Technical Efficacy Thesaurus, Application Domain, Technology Topic, Popular Technical Reports.
© 2025 PatSnap. All rights reserved.Legal|Privacy policy|Modern Slavery Act Transparency Statement|Sitemap|About US| Contact US: help@patsnap.com