Engine lubricating oil filtering material and production technique thereof
A filter material and production process technology, applied in the direction of engine lubrication, engine components, machines/engines, etc., can solve the problems of destroying ecological balance, wasting wood resources, short service life, etc., achieve energy saving, good filtering effect, reduce cost effect
- Summary
- Abstract
- Description
- Claims
- Application Information
AI Technical Summary
Problems solved by technology
Method used
Examples
Embodiment 1
[0017] A. Production of bamboo fiber:
[0018] Take the adult bamboo (3-5 years old) Hsinchu, remove the branches and leaves, use a wire drawing machine to draw bamboo wires with a diameter of 0.6-1mm, then cut them into 3-5mm long bamboo wires with a cutting machine, put the bamboo wires into the softening solution Among them, the softening solution is prepared by mixing 4% sodium hydroxide, 3% sodium sulfite, 15% sodium sulfate, and the rest of water by weight percentage, soaked for 34 hours, and then cooked at 80°C for 2.5 hours Wash with clear water, dry or sun-dry when measuring pH value 6-8, when making water content 15%, make the bamboo fiber that diameter is 0.08-0.2mm with loosening machine repeatedly;
[0019] B. Production of hemp fiber:
[0020] Soak the hemp in 8% sodium hydroxide solution by mass for 75 hours, rinse it with water, dry it when the pH value is 6-9 or dry it naturally, cut it into 3-5mm segments, and loosen it. The machine repeatedly sorts into fl...
Embodiment 2
[0024] A. Production of bamboo fiber:
[0025] Take the adult bamboo (3-5 years old) Hsinchu, remove the branches and leaves, use a wire drawing machine to draw bamboo wires with a diameter of 0.6-1mm, then cut them into 3-5mm long bamboo wires with a cutting machine, put the bamboo wires into the softening solution In this method, the softening solution is prepared by mixing 6% sodium hydroxide, 1% sodium sulfite, 13% sodium sulfate, and the rest of water by weight percentage, soaked for 38 hours, and then cooked at 100 ° C for 1.5 hours Wash with clear water, dry or sun-dry when the pH value is 6-8, make the water content 20%, and repeatedly sort out with a loosening machine to make bamboo fibers with a diameter of 0.08-0.2mm;
[0026] B. Production of hemp fiber:
[0027] Soak apocynum in 12% sodium hydroxide solution for 70 hours, rinse with clean water, dry or dry naturally when the pH value is 6-9, cut into 3-5mm line segments, and loosen The machine repeatedly sorts i...
Embodiment 3
[0031] A. Production of bamboo fiber:
[0032] Take the adult bamboo (3-5 years old) Hsinchu, remove the branches and leaves, use a wire drawing machine to draw bamboo wires with a diameter of 0.6-1mm, then cut them into 3-5mm long bamboo wires with a cutting machine, put the bamboo wires into the softening solution In this method, the softening solution is prepared by mixing 5% sodium hydroxide, 2% sodium sulfite, 14% sodium sulfate, and the rest of water by weight percentage, soaked for 36 hours, and then steamed for 2 hours at a temperature of 90°C Wash with clear water, dry or sun-dry when the pH value is 6-8, make the water content 18%, and repeatedly sort out with a loosening machine to make bamboo fibers with a diameter of 0.08-0.2mm;
[0033] B. Production of hemp fiber:
[0034] Soak the flax in 10% sodium hydroxide solution by mass for 72 hours, rinse it with clean water, dry it when the pH value is 6-9 or dry it naturally, cut it into 3-5mm line segments, and pass ...
PUM
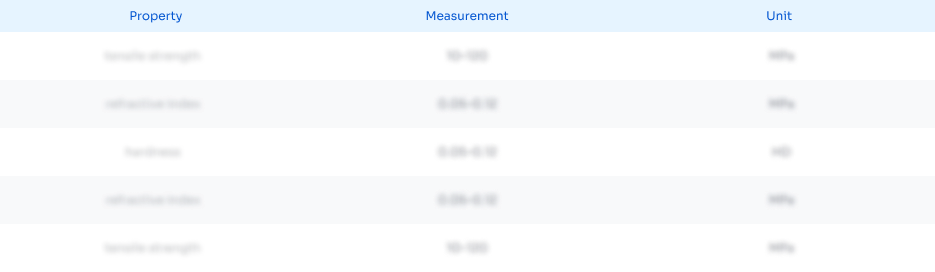
Abstract
Description
Claims
Application Information

- R&D
- Intellectual Property
- Life Sciences
- Materials
- Tech Scout
- Unparalleled Data Quality
- Higher Quality Content
- 60% Fewer Hallucinations
Browse by: Latest US Patents, China's latest patents, Technical Efficacy Thesaurus, Application Domain, Technology Topic, Popular Technical Reports.
© 2025 PatSnap. All rights reserved.Legal|Privacy policy|Modern Slavery Act Transparency Statement|Sitemap|About US| Contact US: help@patsnap.com