Construction method for installing sandwich layer of light composite insulation wall
A technology of composite thermal insulation and construction method, which is applied in the direction of thermal insulation, wall, and building material processing, etc., which can solve the problems of accelerated fixation and unsolved installation and fixation of the core layer, so as to facilitate construction, reduce installation labor consumption, and enhance construction feasibility Effect
- Summary
- Abstract
- Description
- Claims
- Application Information
AI Technical Summary
Problems solved by technology
Method used
Image
Examples
specific Embodiment approach 1
[0024] Specific implementation mode one: see Figure 1 ~ Figure 4 A construction method for installing a core layer in a light-duty composite thermal insulation wall of the present embodiment is that the construction method is to paste and fix the core layer 3-1 on the outside of the load-bearing member 1 of the main building structure; the pasted core layer 3 After -1 is fixed, paste the large core layer 3 within the frame opening of the load-bearing member 1 of the main structure of the building, and leave a space between the large core layer 3 and the core layer 3-1 pasted and fixed on the outside of the load-bearing member 1 of the main structure of the building. If there is a gap, the gap is filled, sealed, bonded and fixed with polyurethane foam glue 3-3, and the joint between adjacent large core layers 3 is fixed with polyurethane foam glue 3-3 foam, filled, sealed and bonded; The load-bearing components 1 of the main structure of the building are beams, plates, columns...
specific Embodiment approach 2
[0025] Embodiment 2: The difference between this embodiment and Embodiment 1 is that both sides or one side or part of the large core layer 3 of this embodiment are pasted and compounded with cement fiberboard or calcium silicate board to form a lightweight core layer 3. Quality prefabricated panels.
Embodiment approach 2
[0026]In Embodiment 2, "or partly pasted and compounded with cement fiberboard or silicon-calcium board" means that the part of the large core layer 3 located at the edge of the door and window opening is pasted and compounded with cement fiberboard or silicon-calcium board, which can strengthen the rigidity of the core layer at the edge of the hole. After the core layer 3 is pasted and compounded with cement fiberboard or calcium silicate board, the rigidity is very large, and it is generally not necessary to support diagonal supports during plastering, which is convenient for plastering construction.
[0027] Embodiments 1 and 2 are suitable for the construction method of installing the core layer of the light-duty composite thermal insulation wall for external thermal insulation. Part of the thickness of the core layer of the external thermal insulation composite wall is located in the opening of the beam-column of the load-bearing member frame of the main structure of the b...
PUM
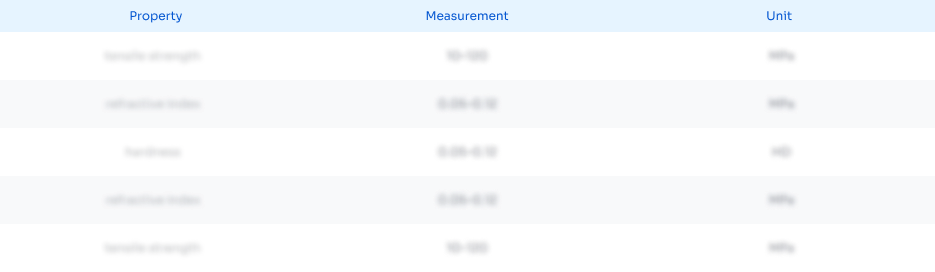
Abstract
Description
Claims
Application Information

- R&D
- Intellectual Property
- Life Sciences
- Materials
- Tech Scout
- Unparalleled Data Quality
- Higher Quality Content
- 60% Fewer Hallucinations
Browse by: Latest US Patents, China's latest patents, Technical Efficacy Thesaurus, Application Domain, Technology Topic, Popular Technical Reports.
© 2025 PatSnap. All rights reserved.Legal|Privacy policy|Modern Slavery Act Transparency Statement|Sitemap|About US| Contact US: help@patsnap.com