Cold roll with high abrasive resistance and high roughness retaining capability and manufacturing method thereof
A technology with high wear resistance and manufacturing method, applied in the direction of rolls, metal rolling, manufacturing tools, etc., can solve the problems of increasing labor intensity of workers, low production efficiency, shutdown, etc., to enhance the roughness retention ability and wear resistance. , The effect of good roughness retention performance and high wear resistance
- Summary
- Abstract
- Description
- Claims
- Application Information
AI Technical Summary
Problems solved by technology
Method used
Image
Examples
Embodiment 1
[0018] The manufacturing method of the cold rolling work roll of this embodiment includes the following steps:
[0019] ① Refining steel to make the chemical composition and content of the steel reach the required range, and use conventional production technology to prepare cold-rolled roll blanks. The specific steps are to use electric arc furnace and LFVD refining furnace to smelt steel materials, mold into electrodes, then anneal the electrode rods, and then remelt the electroslag into an electroslag ingot.
[0020] After the final test, the chemical composition and content in the material of the cold-rolling work roll of this embodiment are as follows (the unit in the table is wt%, and the rest are Fe and unavoidable impurities.):
[0021] C
Si
Mn
Cr
Mo
V
Ni
P
S
0.91
0.30
0.44
4.99
1.1
0.12
0.11
0.010
0.003
[0022] After the composition is qualified, the electroslag ingot is heated, forged into a forging blank, the forging blank is heat-treated, and finall...
Embodiment 2~ Embodiment 8
[0029] The process steps of the manufacturing method of each embodiment are basically the same as that of embodiment 1, and the differences are shown in the following table
[0030]
[0031]
PUM
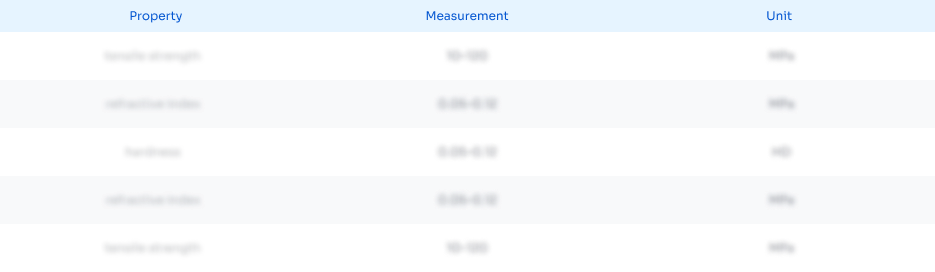
Abstract
Description
Claims
Application Information

- R&D Engineer
- R&D Manager
- IP Professional
- Industry Leading Data Capabilities
- Powerful AI technology
- Patent DNA Extraction
Browse by: Latest US Patents, China's latest patents, Technical Efficacy Thesaurus, Application Domain, Technology Topic, Popular Technical Reports.
© 2024 PatSnap. All rights reserved.Legal|Privacy policy|Modern Slavery Act Transparency Statement|Sitemap|About US| Contact US: help@patsnap.com