Method for separating and extracting tungsten-molybdenum from mixed solution of tungstate-molybdate
A technology of mixed solution and tungsten molybdate, which is applied in the field of separation and extraction of tungsten and molybdenum from mixed solution of tungsten molybdate, can solve the problems of unsuitable mixed solution of tungsten molybdate, and achieves low production cost, strong process adaptability, and easy operation. easy effect
- Summary
- Abstract
- Description
- Claims
- Application Information
AI Technical Summary
Benefits of technology
Problems solved by technology
Method used
Examples
Embodiment 1
[0021] A mixed solution formed by dissolving pure sodium molybdate and pure sodium tungstate, containing Mo35.6g / L, WO 3 10.7g / L, adjust the pH value to 8.3, add calcium carbonate according to 5 times the stoichiometric number of artificial scheelite, stir at 90°C for 1.5 hours to precipitate the tungsten in the solution, filter to obtain artificial scheelite and molybdenum filtrate , the filtrate contains Mo33.8g / L, WO 3 0.1g / L, add hydrochloric acid to artificial scheelite according to 3 times its decomposition chemical reaction, stir at 70°C for 2.0 hours, filter and wash to obtain artificial scheelite, artificial scheelite is obtained by ammonia dissolution and evaporation crystallization Ammonium paratungstate containing 0.01% Mo.
Embodiment 2
[0023] The solution obtained by leaching nickel-molybdenum ore by oxidizing and roasting sodium carbonate and sodium hydroxide mixed alkali, adding acid to adjust the pH to 3.0, first undergoing adsorption transformation with weak base anion resin, and then purifying and removing impurities with magnesium salt, the composition of the ammonium molybdate solution is: Mo 85.3g / L, P 0.01g / L, As 0.004g / L, SiO 2 0.10g / L, WO 3 0.52g / L, pH value 8.2, add calcium carbonate according to 25 times the stoichiometric number of artificial scheelite, stir at 85°C for 2.5 hours to precipitate tungsten in the solution, filter to obtain tungsten-removed slag and tungsten-removed liquid, The composition of tungsten removal slag is WO 3 8.6%, Mo 10.3%, tungsten removal slag stockpile, concentrated recovery of tungsten and molybdenum, the composition of the liquid after tungsten removal: Mo 84.7g / L, P 0.001g / L, As 0.001g / L, SiO 2 0.01g / L, WO 3 0.05g / L, after removing tungsten, add nitric a...
Embodiment 3
[0025] The leaching solution obtained by pressure cooking high molybdenum tungsten concentrate with sodium carbonate contains: WO 3 123g / L, Mo15g / L, pH value 8.2, add magnesium nitrate according to 1.8 times the stoichiometric number of magnesium salt precipitation, stir at 85°C for 1.5 hours, filter to remove P, As and Si, and then press the filtrate to form artificial scheelite Add calcium carbonate at 2.5 times the stoichiometric number of the mineral, stir at 80°C for 3 hours to precipitate tungsten in the solution, filter to obtain artificial scheelite and aluminum-containing filtrate, artificial scheelite is 3 times the stoichiometric number of its decomposition Add hydrochloric acid, stir at 70°C for 2.0 hours, filter and wash to obtain artificial white tungstic acid, artificial white tungstic acid is dissolved in ammonia and crystallized by APT to obtain qualified ammonium tungstate. High-quality ammonium molybdate was obtained by liquid nitric acid precipitation and c...
PUM
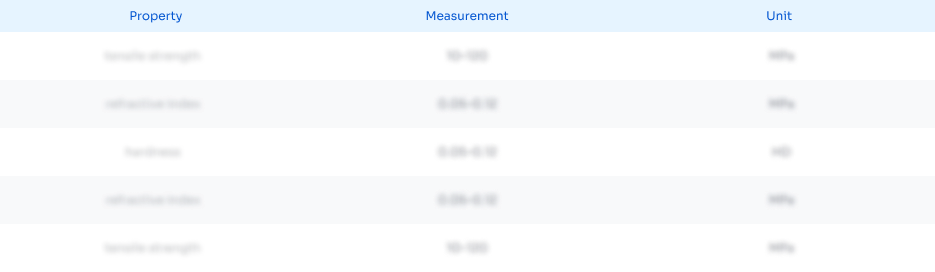
Abstract
Description
Claims
Application Information

- R&D
- Intellectual Property
- Life Sciences
- Materials
- Tech Scout
- Unparalleled Data Quality
- Higher Quality Content
- 60% Fewer Hallucinations
Browse by: Latest US Patents, China's latest patents, Technical Efficacy Thesaurus, Application Domain, Technology Topic, Popular Technical Reports.
© 2025 PatSnap. All rights reserved.Legal|Privacy policy|Modern Slavery Act Transparency Statement|Sitemap|About US| Contact US: help@patsnap.com