Constant-speed transmission shaft with telescopic middle shaft
A constant-speed transmission, intermediate shaft technology, applied in couplings, elastic couplings, mechanical equipment, etc., can solve the problem of poor intermediate shaft slippage, large circumferential transmission clearance, and bending moment at the gearbox end. Large and other problems, to achieve the effect of increased expansion and contraction, large axial space, and smooth transmission
- Summary
- Abstract
- Description
- Claims
- Application Information
AI Technical Summary
Problems solved by technology
Method used
Image
Examples
Embodiment 1
[0055] See Figure 6 , Figure 6-1 and Figure 6-2 , the transmission shaft of the present invention has a center-fixed constant velocity universal joint 10 at the drive wheel end, a center-fixed constant velocity universal joint 20 at the gearbox end, and an intermediate shaft 30. The intermediate shaft includes an intermediate shaft sleeve 31, an intermediate shaft core 33, a retaining Frame 34 and rolling element 32. In this embodiment, rolling element 32 is a steel ball. The mating surface of the intermediate bushing and the intermediate shaft core is a circumferential surface. Corresponding channels for accommodating steel balls are respectively provided. The shape can be a double arc or a single arc, and the cage is used to fix the relative position of the steel balls to ensure the rolling of the steel balls and the transmission of torque.
[0056] Such as Figure 6-1 and Figure 6-2 As shown, the outer diameter of the intermediate shaft sleeve is D1, the outer diame...
Embodiment 2
[0068] The intermediate shaft of the present invention can also adopt another structure, that is, the inner cavity of the intermediate shaft sleeve 31 and the outer shape of the intermediate shaft core 33 are regular polygons, the rolling element 32 adopts a needle roller type, and the corresponding cage 34 is also a regular polygon. The transmission of torque is completed by the corners of the cage.
[0069] The intermediate shaft sleeve, intermediate shaft core and needle roller are installed with a small interference fit, and the outer surface of the intermediate shaft core and the inner surface of the intermediate shaft sleeve are lubricated with grease, which can also ensure the telescopic function of the intermediate shaft, and because the contact surface of the needle roller is large , Strong wear resistance during use.
PUM
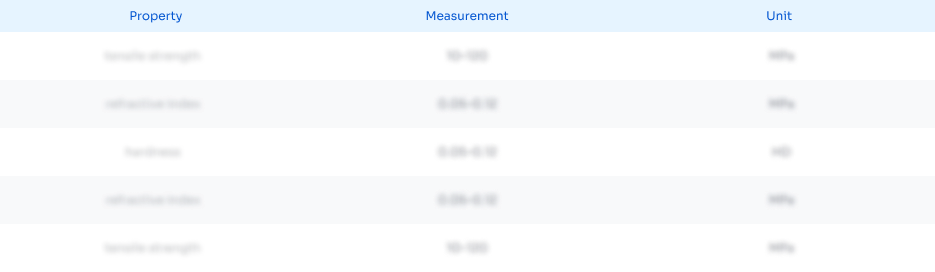
Abstract
Description
Claims
Application Information

- Generate Ideas
- Intellectual Property
- Life Sciences
- Materials
- Tech Scout
- Unparalleled Data Quality
- Higher Quality Content
- 60% Fewer Hallucinations
Browse by: Latest US Patents, China's latest patents, Technical Efficacy Thesaurus, Application Domain, Technology Topic, Popular Technical Reports.
© 2025 PatSnap. All rights reserved.Legal|Privacy policy|Modern Slavery Act Transparency Statement|Sitemap|About US| Contact US: help@patsnap.com