Permanently magnetic strontium ferrite material and preparation method thereof
A strontium ferrite and permanent magnet technology is applied in the field of rapid sintering of permanent magnet strontium ferrite materials after moisture removal, permanent magnet strontium ferrite magnetic materials and their wet forming manufacturing fields, which can solve the problem of high energy It can overcome the problems of energy consumption, poor magnetic properties and crystal structure of sintered ferrite, and achieve the effect of overcoming energy saving and improving structure and magnetic properties.
- Summary
- Abstract
- Description
- Claims
- Application Information
AI Technical Summary
Problems solved by technology
Method used
Image
Examples
Embodiment 1
[0032] A method for preparing a permanent magnet strontium ferrite material by a microwave sintering process, comprising the following steps:
[0033] (1) The strontium-containing ferrite calcined material is mixed with the secondary additives in a ball mill. After wet ball milling, the average particle size of the slurry reaches 0.6um, and then it is dehydrated and separated. The moisture content of the dehydrated slurry is required. at 25%;
[0034] The auxiliary agent added for the second time is CaCO 3 ; The mass ratio of strontium ferrite pre-sintered material to secondary additives is 1:0.142 for strontium ferrite calcined material: secondary additives;
[0035](2), the separated and dehydrated slurry obtained in step (1) is prepared into a green body by wet molding, and the main molding process conditions are: injection time 10s, magnetizing current 150A, holding time 10s, molding pressure 15Mpa;
[0036] (3), place the green body after step (2) molding in natural env...
Embodiment 2
[0041] A method for preparing a permanent magnet strontium ferrite material by a microwave sintering process, comprising the following steps:
[0042] (1) The strontium-containing ferrite calcined material is mixed with the secondary additives in the ball mill. After wet ball milling, the average particle size of the slurry reaches 1.0um and is dehydrated and separated. The moisture content of the dehydrated slurry is required. at 40%;
[0043] The auxiliary agent added for the second time is SiO 2 ; The mass ratio of strontium ferrite pre-sintered material to secondary additives is 1:0.142 for strontium ferrite calcined material: secondary additives;
[0044] (2), the separated and dehydrated slurry obtained in step (1) is prepared into a green body by wet molding, and the main molding process conditions are: injection time 20s, magnetizing current 120A, holding time 20s, molding pressure 20Mpa;
[0045] (3), place the green body after step (2) molding in natural environmen...
Embodiment 3
[0050] A method for preparing a permanent magnet strontium ferrite material by a microwave sintering process, comprising the following steps:
[0051] (1) The strontium-containing ferrite calcined material is mixed with the secondary additives in a ball mill. After wet ball milling, the average particle size of the slurry reaches 0.8um and is dehydrated and separated. The moisture content of the dehydrated slurry is required. at 30%;
[0052] The auxiliary agent added twice is H 3 BO 3 ; The mass ratio of strontium ferrite pre-sintered material to secondary additives is 1:0.142 for strontium ferrite calcined material: secondary additives;
[0053] (2), the separated and dehydrated slurry obtained in step (1) is prepared into a green body by wet molding, and the main molding process conditions are: injection time 15s, magnetizing current 100A, holding time 15s, molding pressure 18Mpa;
[0054] (3), place the green body after step (2) molding in natural environment for 36 hou...
PUM
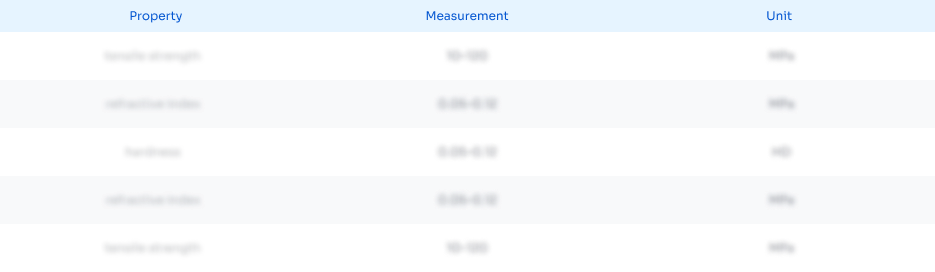
Abstract
Description
Claims
Application Information

- R&D
- Intellectual Property
- Life Sciences
- Materials
- Tech Scout
- Unparalleled Data Quality
- Higher Quality Content
- 60% Fewer Hallucinations
Browse by: Latest US Patents, China's latest patents, Technical Efficacy Thesaurus, Application Domain, Technology Topic, Popular Technical Reports.
© 2025 PatSnap. All rights reserved.Legal|Privacy policy|Modern Slavery Act Transparency Statement|Sitemap|About US| Contact US: help@patsnap.com