Preparation mould of carbon fiber composite material casing of airplane and aircraft and forming method thereof
A composite material and aircraft technology, applied in the field of winding carbon fiber composite material manufacturing, can solve the problems affecting the performance of the shell, fiber breakage, etc., and achieve the effect of reducing weight
- Summary
- Abstract
- Description
- Claims
- Application Information
AI Technical Summary
Problems solved by technology
Method used
Image
Examples
specific Embodiment approach 1
[0032] Specific implementation mode one: the following combination Figure 1 to Figure 6 Describe this embodiment, this embodiment is made up of mold core 1, inner mold 2, outer mold 3, upper cover plate 5, lower cover plate 6 and shaft 7,
[0033] The mold core 1 has a circular table-shaped outer surface and is a hollow structure. The inner mold 2 is set on the side of the outer surface of the mold core 1 and is tightly fixed. The outer ring surface of the inner mold 2 has a plurality of annular clamping grooves 2-1 , the multiple annular slots 2-1 are parallel to each other and are all parallel to the bottom surface of the mold core 1,
[0034] An outer mold 3 is arranged outside the inner mold 2, and the outer mold 3 is coaxial with the inner mold 2. The pressurizing sleeve 4 has a circular table-shaped side wall, the upper end surface is an inwardly protruding ring, and the lower end face is an outwardly protruding ring. The pressure sleeve 4 is set on the outer surface o...
specific Embodiment approach 2
[0041] Embodiment 2: The difference between this embodiment and Embodiment 1 is that the inner mold 2 is assembled from 12 identical longitudinal inner module pieces. Other components and connections are the same as those in Embodiment 1.
[0042] In this embodiment, 12 identical longitudinal inner module pieces are used to assemble the inner mold 2, so that the inner mold 2 can be easily disassembled during use.
specific Embodiment approach 3
[0043] Embodiment 3: The difference between this embodiment and Embodiment 1 is that the material of the outer mold 3 is aluminum alloy. Other components and connections are the same as those in Embodiment 1.
[0044] The outer mold 3 made of aluminum alloy can be used repeatedly, and its inner surface is dense and smooth, which can meet the requirements of the surface flatness of the formed shell.
PUM
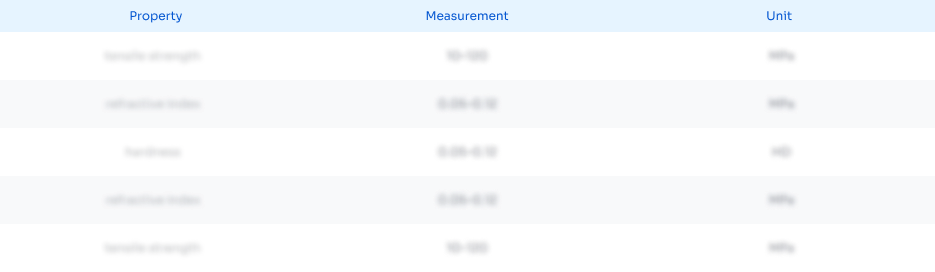
Abstract
Description
Claims
Application Information

- R&D
- Intellectual Property
- Life Sciences
- Materials
- Tech Scout
- Unparalleled Data Quality
- Higher Quality Content
- 60% Fewer Hallucinations
Browse by: Latest US Patents, China's latest patents, Technical Efficacy Thesaurus, Application Domain, Technology Topic, Popular Technical Reports.
© 2025 PatSnap. All rights reserved.Legal|Privacy policy|Modern Slavery Act Transparency Statement|Sitemap|About US| Contact US: help@patsnap.com