Grinding machine of internal combustion abrasive belt of small-sized steel rail
An internal combustion abrasive belt and grinding machine technology, which is applied to tracks, track laying, track maintenance, etc., can solve the problem of high labor intensity of operators, and achieve the effects of small change in the thickness of the abrasive belt, high grinding speed, and convenient debugging.
- Summary
- Abstract
- Description
- Claims
- Application Information
AI Technical Summary
Problems solved by technology
Method used
Image
Examples
Embodiment Construction
[0028] The structure of the rail internal combustion abrasive belt grinding machine is described in detail below in conjunction with the attached drawings:
[0029] Such as figure 1 , figure 2 Shown: this small rail internal combustion abrasive belt grinder has a frame 1 and an abrasive belt drive 3 installed on the frame 1, a grinding depth adjustment device 4, the first and second walking profiling wheels 5, 6 and installed on the Internal combustion engine 2 on belt drive. Grinding machine rides on rail 7 by walking profiling wheel.
[0030] see Figure 4 and Figure 5 , wherein the abrasive belt transmission device 3 is composed of a driving pulley 14, a driven pulley 18, a tension pulley 17, a tensioning device 16 and an abrasive belt 15. The abrasive belt 15 is tightly sleeved on the driving wheel 14, the driven wheel 18 and the tensioning wheel 17 distributed in a triangle, and is tensioned by the tensioning device 16 connected with the tensioning wheel 17. The o...
PUM
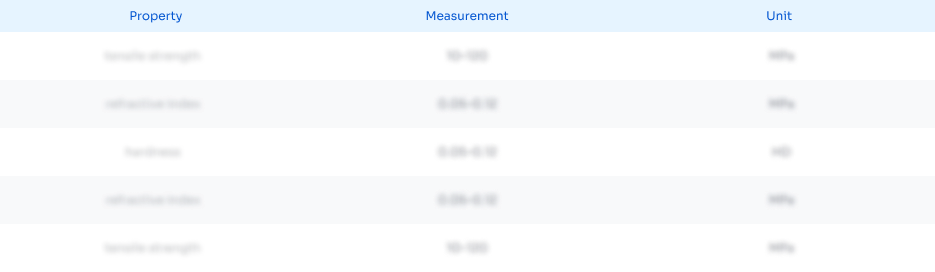
Abstract
Description
Claims
Application Information

- Generate Ideas
- Intellectual Property
- Life Sciences
- Materials
- Tech Scout
- Unparalleled Data Quality
- Higher Quality Content
- 60% Fewer Hallucinations
Browse by: Latest US Patents, China's latest patents, Technical Efficacy Thesaurus, Application Domain, Technology Topic, Popular Technical Reports.
© 2025 PatSnap. All rights reserved.Legal|Privacy policy|Modern Slavery Act Transparency Statement|Sitemap|About US| Contact US: help@patsnap.com