Separation method of m-cresol and p-cresol mixture
A separation method and a technology for mixing cresols, which are applied in chemical instruments and methods, preparation of organic compounds, organic chemistry, etc., to achieve the effects of high atomic utilization, low raw material consumption and production cost, and high reaction conversion rate.
- Summary
- Abstract
- Description
- Claims
- Application Information
AI Technical Summary
Problems solved by technology
Method used
Examples
Embodiment 1
[0017] Put 1080kg m-p-cresol mixture (m-cresol mass content is 62.90%, p-cresol mass content is 37.06%), 20kg cation exchange resin is put into the reaction kettle, start stirring, heat up to 125 ℃; Then 924kg methyl tertiary Butyl ether was continuously added dropwise into the reaction kettle within 3 hours, and the reaction temperature was maintained at 125±2°C. After the dropwise addition, the temperature of the kettle was raised to 135°C and maintained for 1 hour; Pressure rectification, obtain the 6-tert-butyl m-cresol 943.8kg that purity is 99.73%, the 2-tert-butyl-p-cresol 558.5kg that purity is 99.57%;
[0018] Put 943.8kg of 6-tert-butyl m-cresol and 20kg of cation exchange resin into the reaction kettle, start stirring, raise the temperature to 100°C, and keep it warm for three hours; the isobutene produced by decomposition is recovered by freezing and compressing to obtain 273.2kg of isobutene; Pressure rectification, obtaining purity is 99.58% m-cresol 557.8kg;
...
Embodiment 2
[0021] 1080kg m-p-cresol mixture (m-cresol mass content is 62.90%, p-cresol mass content is 37.06%), 20kg cation exchange resin is put into reactor, start stirring, be warming up to 70 ℃; Add it dropwise into the reaction kettle continuously within 1 hour, maintain the reaction temperature at 70±2°C, after the dropwise addition, raise the reaction temperature to 80°C, and maintain the reaction for 1 hour; after the reaction is completed, filter the catalyst, and rectify the mixture under reduced pressure to obtain 950.5kg of 6-tert-butyl m-cresol with a purity of 99.65%, and 557.2 kg of 2-tert-butyl-p-cresol with a purity of 99.51%;
[0022] Put 950.5kg of 6-tert-butyl m-cresol and 20kg of cation exchange resin into the reaction kettle, start stirring, raise the temperature to 100°C, and keep it warm for three hours; the isobutene produced by decomposition is recovered by freezing and compressing to obtain 276.1kg of isobutene; Pressure rectification, obtaining purity is 99.63...
Embodiment 3
[0025] Put 1080kg of m-p-cresol mixture (the mass content of m-cresol is 62.90%, and the mass content of p-cresol is 37.06%), and 20kg of loaded mesoporous molecular sieve catalysts are put into the reactor, and the stirring is started, and the temperature is raised to 125°C; Continuously drop tert-butyl ether into the reaction kettle within 3 hours, maintain the reaction temperature at 125±2°C, after the dropwise addition, raise the reaction temperature to 135°C, and maintain the reaction for 1 hour; The liquid was rectified under reduced pressure to obtain 949.3kg of 6-tert-butyl m-cresol with a purity of 99.70%, and 560.3 kg of 2-tert-butyl-p-cresol with a purity of 99.69%;
[0026] Put 949.3kg of 6-tert-butyl m-cresol and 20kg of loaded mesoporous molecular sieve catalyst into the reaction kettle, start stirring, raise the temperature to 100°C, and keep it warm for three hours; the isobutene produced by decomposition is recovered by freezing and compressing to obtain 274.3k...
PUM
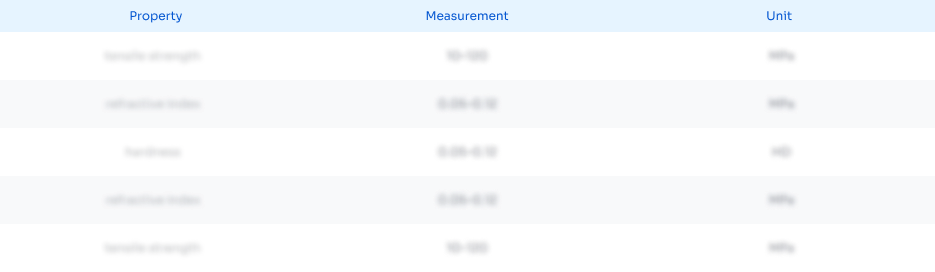
Abstract
Description
Claims
Application Information

- R&D
- Intellectual Property
- Life Sciences
- Materials
- Tech Scout
- Unparalleled Data Quality
- Higher Quality Content
- 60% Fewer Hallucinations
Browse by: Latest US Patents, China's latest patents, Technical Efficacy Thesaurus, Application Domain, Technology Topic, Popular Technical Reports.
© 2025 PatSnap. All rights reserved.Legal|Privacy policy|Modern Slavery Act Transparency Statement|Sitemap|About US| Contact US: help@patsnap.com