Method for producing alumina with aluminum-containing metallurgical material
An aluminum metallurgy and alumina technology, applied in the field of alumina production from aluminum-containing metallurgical materials, can solve the problems of weak market competitiveness and high alumina production cost, and achieve the effects of good product quality, fast decomposition speed and strong process adaptability.
- Summary
- Abstract
- Description
- Claims
- Application Information
AI Technical Summary
Problems solved by technology
Method used
Examples
Embodiment 1
[0037] Add sulfuric acid to 1000g of gibbsite according to 1.2 times the stoichiometric amount, liquid-solid ratio L / S 3: 1mL / g, stir at 95°C for 3 hours, filter; stir the crude aluminum sulfate solution and add sodium hydroxide to adjust the pH to 2.6, Purify at 85°C for 1 hour, filter; add sodium carbonate to the refined aluminum sulfate solution to neutralize to pH 5.5, stir at 95°C for 1 hour to precipitate aluminum hydroxide, filter and wash; calcinate aluminum hydroxide at 850°C for 2 hours to obtain Al with a purity of 99.1% 2 o 3 Product; the sodium sulfate filtrate obtained by sinking aluminum is added into ammonium bicarbonate according to 1.4 times of the stoichiometric number of sodium bicarbonate, stirred at 55°C for 1 hour, and filtered to obtain sodium bicarbonate and ammonium sulfate solution; the ammonium sulfate solution is used as anolyte, and 0.2mol / L sulfuric acid solution is used as the catholyte, and the catholyte and the anolyte are separated by an anio...
Embodiment 2
[0039] Contains Al 2 o 3 Add sulfuric acid to 2000g of 30% fly ash according to 1.4 times of the stoichiometric amount, stir, and roast at 250°C for 2 hours; split the calcined sand into two, liquid-solid ratio L / S 2:1mL / g, soak in water at 100°C for 1 hour, filter; the filtrate is cooled and crystallized, the mother liquor is used for the leaching of the next batch of calcined sand, and the aluminum sulfate crystals are dissolved by adding water and stirring at 100°C; hours, filtered and washed to obtain aluminum hydroxide and sodium sulfate solution; aluminum hydroxide was calcined at 1000°C for 2 hours to obtain Al with a purity of 99.6%. 2 o 3 Product: Add ammonium bicarbonate to the sodium sulfate filtrate according to 1.2 times the stoichiometric number of sodium bicarbonate formation, stir at 50°C for 1 hour, filter to obtain sodium bicarbonate and ammonium sulfate solution; ammonium sulfate solution is 1.1 times the stoichiometric number to form gypsum Add lime, sti...
Embodiment 3
[0041] Add 800g of boehmite to 1.1 times of the stoichiometric amount, add sulfuric acid and stir, and roast at 220°C for 1 hour; the liquid-solid ratio of calcined sand is L / S 4:1mL / g, soak in water at 90°C for 1 hour, filter; the filtrate is cooled Crystallization, the mother liquor is used for the leaching of the next batch of calcined sand, the aluminum sulfate crystals are dissolved by adding water and stirring at 95°C; the heavy aluminum sulfate solution is added to the sodium bicarbonate obtained in Example 2 to neutralize to pH 6.2, stirred at 85°C for 1 hour, filtered and washed to obtain hydrogen Alumina and sodium sulfate solution; calcining aluminum hydroxide at 950°C for 2 hours to obtain Al with a purity of 99.7% 2 o 3 Product; sodium bicarbonate filtrate is added into ammonium bicarbonate according to 1.2 times the stoichiometric number of sodium bicarbonate formation, stirred at 50°C for 1 hour, and filtered to obtain sodium bicarbonate and ammonium sulfate sol...
PUM
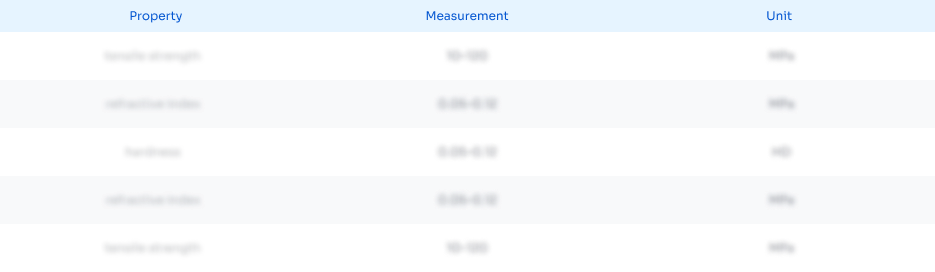
Abstract
Description
Claims
Application Information

- R&D
- Intellectual Property
- Life Sciences
- Materials
- Tech Scout
- Unparalleled Data Quality
- Higher Quality Content
- 60% Fewer Hallucinations
Browse by: Latest US Patents, China's latest patents, Technical Efficacy Thesaurus, Application Domain, Technology Topic, Popular Technical Reports.
© 2025 PatSnap. All rights reserved.Legal|Privacy policy|Modern Slavery Act Transparency Statement|Sitemap|About US| Contact US: help@patsnap.com