Antioxidation aluminium unburned carbon brick and preparation method thereof
A technology for resisting alumina and carbon bricks is applied in the field of aluminum non-burning carbon bricks, which can solve the problems of loss of excellent performance of carbon-containing refractories, difficult wettability of slag, etc., so as to improve oxidation resistance and flexural strength. , the effect of enhanced liquidity
- Summary
- Abstract
- Description
- Claims
- Application Information
AI Technical Summary
Problems solved by technology
Method used
Image
Examples
Embodiment 1
[0027] Embodiment 1 anti-alumina silicon-carbon brick (anti-oxidation Al 2 o 3 -SiC-C brick)
[0028] (1) The ratio of raw materials is shown in Table 1
[0029] (2) The preparation method is as follows:
[0030] 1) According to the ratio in Table 1, weigh brown corundum, ferrosilicon nitride and phenolic resin, pre-mix and grind in a sand mixer for 8-10 minutes, then add the remaining raw materials, and mix and grind for 12-15 minutes;
[0031] 2) Put the mixed material into the mold, pressurize it on a 500-ton to 800-ton friction brick press to make a green body;
[0032] 3) Send the green body to the drying kiln for drying. The hot air inlet temperature of the drying kiln is 40-60°C, the temperature of the heat preservation interval is 180°C, the outlet temperature is 40-60°C, and the drying time is not less than 16 hours. The length of the drying kiln is not less than 24 meters, and the interval between carts is 40 to 70 minutes per cart.
[0033] The test results of ...
Embodiment 2
[0036] Embodiment 2 anti-alumina silicon-carbon brick (anti-oxidation Al 2 o 3 -SiC-C brick)
[0037] (1) The ratio of raw materials is shown in Table 1
[0038] (2) The preparation method is as follows:
[0039] 1) According to the ratio in Table 1, weigh brown corundum, ferrosilicon nitride and phenolic resin, pre-mix and grind in a sand mixer for 8-10 minutes, then add the remaining raw materials, and mix and grind for 12-15 minutes;
[0040] 2) Put the mixed material into the mold, pressurize it on a 500-ton to 800-ton friction brick press to make a green body;
[0041] 3) Send the green body to the drying kiln for drying. The hot air inlet temperature of the drying kiln is 40-60°C, the temperature of the heat preservation interval is 180°C, the outlet temperature is 40-60°C, and the drying time is not less than 16 hours. The length of the drying kiln is not less than 24 meters, and the interval between carts is 40 to 70 minutes per cart.
[0042] The test results of ...
Embodiment 3
[0043] Embodiment 3 anti-oxidation alumina magnesia carbon brick (anti-oxidation Al 2 o 3 -MgO-C brick)
[0044] (1) The ratio of raw materials is shown in Table 2
[0045] (2) The preparation method is as follows:
[0046] 1) According to the ratio in Table 2, weigh brown corundum, fused magnesia, ferrosilicon nitride and phenolic resin, pre-mix and grind in the sand mixer for 8-10 minutes, then add the remaining raw materials, and mix and grind for 12 minutes. ~15 minutes;
[0047] 2) Put the mixed material into the mold, pressurize it on a 500-ton to 800-ton friction brick press to make a green body;
[0048] 3) Send the green body to the drying kiln for drying. The hot air inlet temperature of the drying kiln is 40-60°C, the temperature of the heat preservation interval is 180°C, the outlet temperature is 40-60°C, and the drying time is not less than 16 hours. The length of the drying kiln is not less than 24 meters, and the interval between carts is 40 to 70 minutes ...
PUM
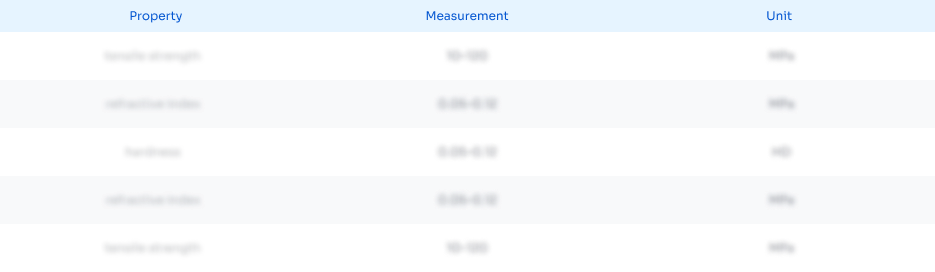
Abstract
Description
Claims
Application Information

- R&D Engineer
- R&D Manager
- IP Professional
- Industry Leading Data Capabilities
- Powerful AI technology
- Patent DNA Extraction
Browse by: Latest US Patents, China's latest patents, Technical Efficacy Thesaurus, Application Domain, Technology Topic, Popular Technical Reports.
© 2024 PatSnap. All rights reserved.Legal|Privacy policy|Modern Slavery Act Transparency Statement|Sitemap|About US| Contact US: help@patsnap.com