Deep hole processing tool structure
A tooling and deep hole technology, which is applied in the field of tooling structure for deep hole processing inside the workpiece, can solve the problems of difficult machining of the box, difficult machining of deep holes inside the spindle box, and increased processing difficulty, and achieve simple assembly, reasonable structure, The effect of improving processing efficiency
- Summary
- Abstract
- Description
- Claims
- Application Information
AI Technical Summary
Problems solved by technology
Method used
Image
Examples
Embodiment Construction
[0012] The present invention will be further described below in conjunction with the embodiments in the drawings:
[0013] Such as Figure 1 ~ Figure 3 Shown: including the first positioning sleeve 1, the first fixed shaft 2, the first positioning plate 3, the second positioning sleeve 4, the first spacer 5, the second positioning plate 6, the second spacer 7, the first flange Cover 8, second flange cover 9, second fixed shaft 10, tool holder 11, boring shaft 12, first set 13, second set 14, third set 15, pad 16, lock nut 17, and box 18 .
[0014] The present invention adopts the first positioning sleeve 1, the second positioning sleeve 4 and the first flange cover 8 to be fastened by screws on the machined surface at the position of the first fixed shaft 2 of the box body 18. The first fixed shaft 2 It is matched with the inner holes of the first positioning sleeve 1, the second positioning sleeve 4 and the first flange cover 8, and is connected with the first flange cover 8 by ...
PUM
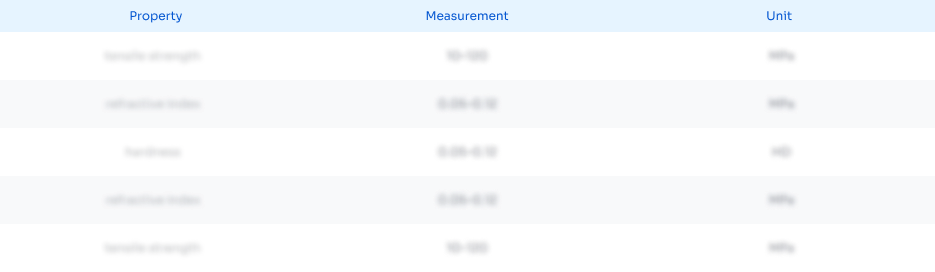
Abstract
Description
Claims
Application Information

- Generate Ideas
- Intellectual Property
- Life Sciences
- Materials
- Tech Scout
- Unparalleled Data Quality
- Higher Quality Content
- 60% Fewer Hallucinations
Browse by: Latest US Patents, China's latest patents, Technical Efficacy Thesaurus, Application Domain, Technology Topic, Popular Technical Reports.
© 2025 PatSnap. All rights reserved.Legal|Privacy policy|Modern Slavery Act Transparency Statement|Sitemap|About US| Contact US: help@patsnap.com