Redundancy-driven three-degree-of-freedom parallel mechanism
A degree of freedom, parallel technology, used in metal processing machinery parts, large fixed members, metal processing equipment, etc., can solve the problems of irregular working space, small working space, complex CNC programming, etc. and improve the accuracy, realize the effect of modularization
- Summary
- Abstract
- Description
- Claims
- Application Information
AI Technical Summary
Problems solved by technology
Method used
Image
Examples
Embodiment 1
[0025] The structure of the drive redundant three-degree-of-freedom parallel mechanism in this embodiment is as follows: figure 1 Shown, comprise fixed platform 11, fixed platform 17, fixed platform 112, moving platform 18 and first, second, the third branch chain, described three branch chains are respectively connected to fixed platform 11, fixed platform 17, fixed platform 112 Between the moving platform 18 and the platform 11, the fixed platform 17, the fixed platform 112 and the moving platform 18 constitute a space closed-loop mechanism.
[0026] The first and second branch chains are PRRR type motion branch chains, including slider 12, slider 16, connecting rod 13, connecting rod 15, U-shaped frame 14 and kinematic pairs. There are four kinematic pairs, one is to be connected to the mobile pair (P) between the fixed platform 11, the fixed platform 17 and the slide block 12, the slide block 16, and one is to be connected to the slide block 12, the slide block 16 and the ...
Embodiment 2
[0029] The structure of the drive redundant three-degree-of-freedom parallel mechanism in this embodiment is as follows: figure 2As shown, the difference between this mechanism and Embodiment 1 is that the placement direction of slide table 21 is perpendicular to the placement direction of slide table 110 in Embodiment 1. At this time, the direction of the moving pair on slide table 21 is the same as that of Embodiment 1. 1 is connected to the plane where the direction of movement of the moving pair between the fixed platform 11, the fixed platform 17 and the slide block 12 and the slide block 16 is vertical.
Embodiment 3
[0031] The structure of the drive redundant three-degree-of-freedom parallel mechanism in this embodiment is as follows: image 3 As shown, the difference between this mechanism and Embodiment 1 is that the placement direction of the fixed platform 31 and the fixed platform 32 is perpendicular to the placement direction of the fixed platform 11 and the fixed platform 17 in Embodiment 1, and the fixed platform 31 and the fixed platform 32 The moving direction of the moving pair on the top is on a straight line, and this straight line direction is parallel to the moving direction of the moving pair connected between the fixed platform 112 and the slide table 110 in Embodiment 1.
PUM
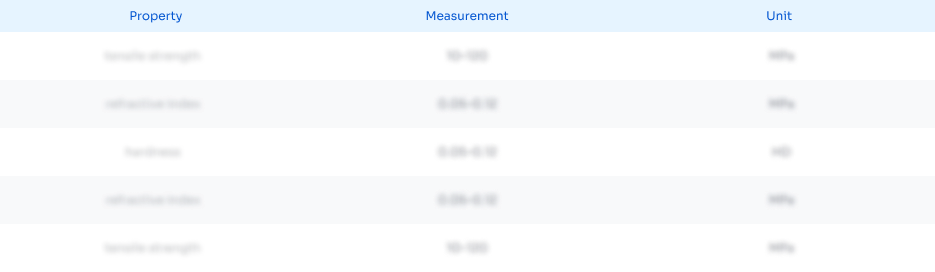
Abstract
Description
Claims
Application Information

- R&D
- Intellectual Property
- Life Sciences
- Materials
- Tech Scout
- Unparalleled Data Quality
- Higher Quality Content
- 60% Fewer Hallucinations
Browse by: Latest US Patents, China's latest patents, Technical Efficacy Thesaurus, Application Domain, Technology Topic, Popular Technical Reports.
© 2025 PatSnap. All rights reserved.Legal|Privacy policy|Modern Slavery Act Transparency Statement|Sitemap|About US| Contact US: help@patsnap.com