Close-fitting combined structure of cooling fin and heat pipe of radiator
A combined structure and heat sink technology, applied in heat exchange equipment and other directions, can solve the problems of increased liquid flow resistance and other issues
- Summary
- Abstract
- Description
- Claims
- Application Information
AI Technical Summary
Problems solved by technology
Method used
Image
Examples
Embodiment Construction
[0040] The invention will be further described below in conjunction with the accompanying drawings and specific embodiments.
[0041] Such as Figure 1 to Figure 5 As shown, the present invention is a tight-fit combination structure of radiator fins and heat pipes, including a plurality of heat sinks 1, more than one heat pipe 2 and a base 3, wherein:
[0042] A plurality of heat sinks 1, such as image 3 , Figure 4 As shown, the upper end surface of each heat sink 1 is provided with more than one concave hole groove 11, and the bottom of the concave hole groove 11 all extends to form a special-shaped hole 111 different from the shape of the heat pipe body (such as an octagonal hole as shown in the figure, or various polygonal holes, or other regular or irregular almost-shaped holes), and a plurality of adjacent concave holes are used in series to form a long groove 110 that allows the stamping die 4 to pass through (Such as Figure 5 , Figure 7 ).
[0043] More than o...
PUM
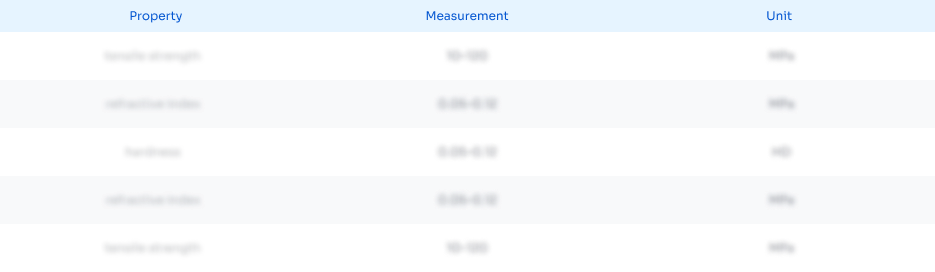
Abstract
Description
Claims
Application Information

- Generate Ideas
- Intellectual Property
- Life Sciences
- Materials
- Tech Scout
- Unparalleled Data Quality
- Higher Quality Content
- 60% Fewer Hallucinations
Browse by: Latest US Patents, China's latest patents, Technical Efficacy Thesaurus, Application Domain, Technology Topic, Popular Technical Reports.
© 2025 PatSnap. All rights reserved.Legal|Privacy policy|Modern Slavery Act Transparency Statement|Sitemap|About US| Contact US: help@patsnap.com