Method for preprocessing coal tar
A technology for coal tar and pretreatment, which is applied in the direction of multi-stage series refining process treatment, etc., can solve the problems of unsuitable coal tar pretreatment, low degree of automation, high labor intensity, etc. Low-intensity, highly automated effects
- Summary
- Abstract
- Description
- Claims
- Application Information
AI Technical Summary
Problems solved by technology
Method used
Examples
Embodiment 1
[0023] Mix 1000g of full-fraction medium and low-temperature coal tar with 500g of catalytic diesel oil (mass ratio 1:0.5), heat the resulting mixture to 100°C, and use a horizontal spiral sedimentation centrifuge for centrifugation to separate 1423g of catalytic diesel solubles And extract insoluble matter 77g. The extracted insolubles were mixed with 308g of benzene (mass ratio 1:4), and the resulting mixture was heated to 50°C, and centrifuged on a horizontal spiral sedimentation centrifuge to separate 356g of benzene solubles and 29g of raffinate. Catalyzed diesel solubles and benzene recovery solubles are uniformly mixed as feed components for coal tar hydrotreating. The impurity content and extraction yield of coal tar after pretreatment are shown in Table 1.
Embodiment 2
[0025] Mix 1000g coal tar heavy oil (>350°C fraction) with 3000g coal tar hydrogenation unit hydrogenated oil >160°C fraction (mass ratio 1:3), heat the mixture to 150°C, and use a horizontal screw The sedimentation centrifuge performs the first centrifugation, and separates 3548g of distillate soluble matter and 452g of extracted insoluble matter. The extracted insoluble matter is mixed with 904g of hydrogenated oil and diesel fraction from the coal tar hydrogenation unit, the resulting mixture is heated to 150°C, and the second centrifugation is carried out on a disc-type continuous centrifuge with a higher separation factor, and the final separation 1110g diesel oil soluble matter and 246g extraction insoluble matter were obtained. The extracted insolubles were mixed with 246g of toluene (mass ratio 1:1), and the resulting mixture was heated to 100°C, and centrifuged in a horizontal spiral sedimentation centrifuge to separate 457g of toluene solubles and 35g of raffinate. ...
Embodiment 3
[0027] Mix 1000g of coal tar gasoline and diesel fraction (9 -C 12 aromatics solvent oil (mass ratio 1:2) mixed, the resulting mixture was heated to 150 ° C, and centrifuged in a horizontal spiral sedimentation centrifuge to separate 852 g of heavy aromatics solubles and 132 g of raffinate. The raffinate was mixed with 264g of toluene again, and the resulting mixture was heated to 100°C, and then centrifuged for the second time on a disc-type continuous centrifuge with a higher separation factor, and finally 354g of toluene soluble matter and 22g of raffinate were separated. The solubles of hydrotreated diesel oil, heavy aromatics, and solubles recovered from toluene were evenly mixed as feed components for coal tar hydrogenation upgrading. The impurity content and extraction yield of coal tar after pretreatment are shown in Table 1.
PUM
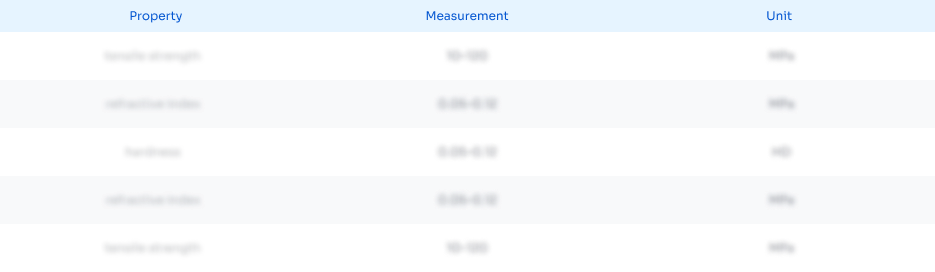
Abstract
Description
Claims
Application Information

- R&D
- Intellectual Property
- Life Sciences
- Materials
- Tech Scout
- Unparalleled Data Quality
- Higher Quality Content
- 60% Fewer Hallucinations
Browse by: Latest US Patents, China's latest patents, Technical Efficacy Thesaurus, Application Domain, Technology Topic, Popular Technical Reports.
© 2025 PatSnap. All rights reserved.Legal|Privacy policy|Modern Slavery Act Transparency Statement|Sitemap|About US| Contact US: help@patsnap.com