Laser electrolysis jet flow combined working time-shared control system and control method
A composite processing and time-sharing control technology, applied in the field of laser electrolytic jet composite processing, can solve the problems of low electrolytic processing voltage and inability to eradicate the recasting layer, and achieve high surface quality, high comprehensive processing efficiency, and high efficiency.
- Summary
- Abstract
- Description
- Claims
- Application Information
AI Technical Summary
Problems solved by technology
Method used
Image
Examples
Embodiment 1
[0017] Example 1, time-sharing processing of laser-direct current electrolysis jet. When the switch S2 in the microprocessor control circuit III is closed and the S1 switches 1 and 3 are connected, a high-level signal is input to the power amplifier circuit IV, so that the compound transistor Q1 and the power switch tube Q2 of the power amplifier circuit IV are turned on, and the conduction of Q2 By connecting the nozzle to the negative pole of the power supply, a current loop is formed between the negative pole of the power supply, the nozzle, the spray liquid, the workpiece, and the positive pole of the power supply, and the generated DC current performs anodic electrolytic dissolution on the workpiece, that is, DC electrolytic machining. At the same time of DC electrolytic jet processing, the level signal waveforms of the output terminals B and C of the interface circuit of the microprocessor control circuit III are time-sharing, see image 3 , so that laser processing and ...
Embodiment 2
[0019] Example 2, time-sharing processing of laser-pulse electrolysis jet. When the switch S2 in the microprocessor control circuit III is closed and the S1 switches 2 and 3 are connected, the pulse signal is input to the power amplifier circuit IV, so that the compound transistor Q1 and the power switch tube Q2 of the power amplifier circuit IV generate pulse conduction, and the conduction of Q2 By connecting the nozzle to the negative pole of the power supply, a pulse current is generated in the negative pole of the power supply, the nozzle, the jet liquid beam, the workpiece, and the positive pole of the power supply, and the pulse current performs pulse electrolysis on the workpiece. At the same time of pulse electrolytic jet processing, the level signal waveforms of the output terminals B and C of the interface circuit of the microprocessor control circuit III are time-sharing, see image 3 , so that laser processing and pulse electrolytic jet processing can be carried ou...
PUM
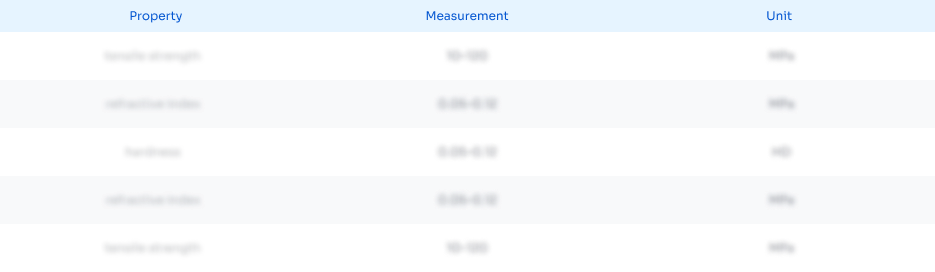
Abstract
Description
Claims
Application Information

- Generate Ideas
- Intellectual Property
- Life Sciences
- Materials
- Tech Scout
- Unparalleled Data Quality
- Higher Quality Content
- 60% Fewer Hallucinations
Browse by: Latest US Patents, China's latest patents, Technical Efficacy Thesaurus, Application Domain, Technology Topic, Popular Technical Reports.
© 2025 PatSnap. All rights reserved.Legal|Privacy policy|Modern Slavery Act Transparency Statement|Sitemap|About US| Contact US: help@patsnap.com