Production line and process for punching U-shaped beam
A production line and U-shaped technology, which is applied in the field of U-shaped beam punching, can solve the problems of high cost and complex structure of the production line, and achieve the effects of reducing production costs, convenient operation, and simplifying subsequent processes
- Summary
- Abstract
- Description
- Claims
- Application Information
AI Technical Summary
Problems solved by technology
Method used
Image
Examples
Embodiment 1
[0033] Reference attached figure 2 , an airfoil sample punching machine D, the airfoil sample punching machine D includes a frame 11, two sets of detection devices, two sets of adjustment structures, two sets of sample impulse power heads and a lifting device, wherein the detection device is used It is used to detect the height deviation of the left and right airfoils of the U-shaped beam; the adjustment structure is installed at the lower part of the detection device to adjust the distance between the two sets of detection devices and the left and right airfoils; two sets of sample impulse heads are respectively used for the U-shaped beam The marking on the left and right airfoils is located under the detection device; the lifting device is used to adjust the height of the power head of the sample punch relative to the airfoil according to the detected height deviation of the left and right airfoils, and is located under the power head of the sample punch.
[0034] The detec...
Embodiment 2
[0042] Such as image 3 The lifting device of the airfoil sample punching machine D shown includes two lifting structures 9 respectively connected to the punch cylinder 6 and two servo motors 10 for controlling the movement of the lifting structure 9 in the Y direction. Other parts of the structure embodiment 1 .
[0043] The working principle of the lifting device: when the detection device measures the deviation value and compensates the deviation value to the coordinate value in the Z direction, the left and right sample punches control the movement of the lifting structure 9 through their respective servo motors 10 to drive the sample punching power head to feed, and then use the punch The head cylinder is used as the power to drive the left and right sample punches to mark with sample punches at the positions of the left and right wing faces.
[0044] In Embodiment 1, a servo motor 10 drives the left and right sample impulse heads 15. When the heights of the left and rig...
PUM
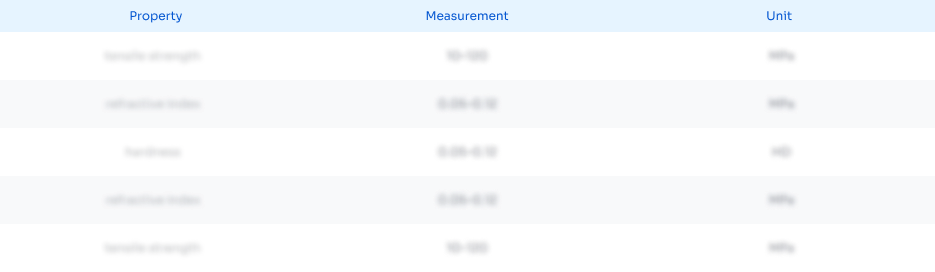
Abstract
Description
Claims
Application Information

- R&D
- Intellectual Property
- Life Sciences
- Materials
- Tech Scout
- Unparalleled Data Quality
- Higher Quality Content
- 60% Fewer Hallucinations
Browse by: Latest US Patents, China's latest patents, Technical Efficacy Thesaurus, Application Domain, Technology Topic, Popular Technical Reports.
© 2025 PatSnap. All rights reserved.Legal|Privacy policy|Modern Slavery Act Transparency Statement|Sitemap|About US| Contact US: help@patsnap.com