Negative energy consumption dioxin emission reducing system of sintering machine and method thereof
A technology of dioxin and energy consumption, applied in separation methods, chemical instruments and methods, dispersed particle separation, etc., can solve the problems of difficulty in large-scale promotion, unsuitable sintering, high operating costs, and achieve obvious energy-saving effect and emission reduction. Improve the effect and ensure the effect of the same quality
- Summary
- Abstract
- Description
- Claims
- Application Information
AI Technical Summary
Problems solved by technology
Method used
Image
Examples
Embodiment Construction
[0049] The present invention will be described in detail below in conjunction with the accompanying drawings and embodiments.
[0050] see first figure 2 , a sintering machine negative energy consumption dioxin emission reduction system of the present invention is mainly composed of switching valve 1, switching valve 2, air mixing valve 3, dust collector 4, switching valve 5, waste heat boiler 6, switching valve 7, bypass Pipe 8, switching valve 9, bypass flue 10, circulating smoke pipe 11, circulating fan 12, circulating smoke hood 13, dust collector, fan, desulfurization tower and chimney.
[0051] The present invention divides the exhaust box at the lower part of the sintering trolley into a high-dioxin area and a low-dioxin area, collects the flue gas generated in the high-dioxin area separately, and then circulates this part of the flue gas to the upper part of the sintering machine as a Combustion air, dioxins are decomposed at high temperature, so as to achieve the purp...
PUM
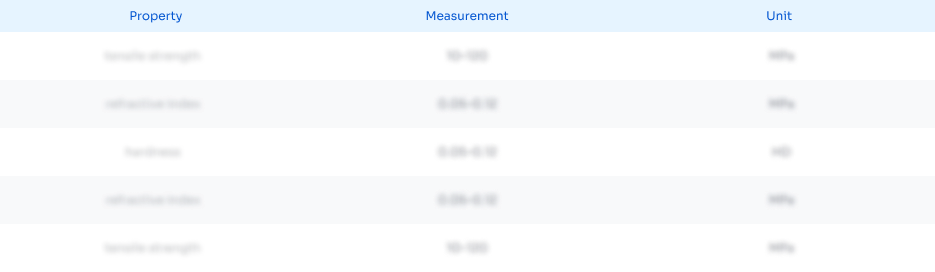
Abstract
Description
Claims
Application Information

- R&D
- Intellectual Property
- Life Sciences
- Materials
- Tech Scout
- Unparalleled Data Quality
- Higher Quality Content
- 60% Fewer Hallucinations
Browse by: Latest US Patents, China's latest patents, Technical Efficacy Thesaurus, Application Domain, Technology Topic, Popular Technical Reports.
© 2025 PatSnap. All rights reserved.Legal|Privacy policy|Modern Slavery Act Transparency Statement|Sitemap|About US| Contact US: help@patsnap.com