Iron-based magnetostrictive alloy wire and production method thereof
A magnetostrictive and alloy wire technology, applied in the direction of magnetic materials, magnetic objects, electrical components, etc., can solve the problems of undiscovered iron-based magnetostrictive wire patents, etc. good strength effect
- Summary
- Abstract
- Description
- Claims
- Application Information
AI Technical Summary
Problems solved by technology
Method used
Image
Examples
Embodiment 1
[0030] Example 1: Fe 78 Ga 17 Al 4 Tb 1 Magnetostrictive filament
[0031] Weigh the raw materials required for the design components with an electronic balance, and use Fe with a purity of more than 99%, 99.99% Ga, 99.5% Al, 99.9% Tb, and add 2% Ga and Tb. Put the good raw materials into the crucible and vacuum to 3×10 -3 Pa, pass argon protection and heating to form an alloy, and after melting, refining for 2 to 3 minutes, and then pouring into an alloy ingot;
[0032] The alloy ingot is hot forged at 1050°C into a 20×20mm billet to provide raw materials suitable for rolling;
[0033] The forged alloys were hot rolled at 1000°C and warm rolled at 500°C, respectively, and rolled into wire rods with a diameter of 8mm;
[0034] The wire rod rolled into φ8mm is cold drawn at 10-35°C, the total number of passes is 18, and the wire rod with φ2.5mm is cold drawn.
[0035] image 3 .for Fe 78 Ga 17 Al 4 Tb 1 The room temperature magnetostriction curve of the alloy wire s...
Embodiment 2
[0036] Example 2: Fe 76.2 Ga 18 Mn 4 V 1 Ce 0.8 Magnetostrictive filament
[0037] Weigh the raw materials required for the design components with an electronic balance, in which Fe with a purity greater than 99%, Ga with a purity of 99.99%, Mn and V with a purity of 99.9% are used, and the burning loss of 3% Ga and Ce is added. Put it in a crucible and vacuum to 3×10 -3 Pa, pass argon protection and heating to form an alloy, and after melting, refining for 2 to 3 minutes, and then pouring into an alloy ingot;
[0038] The alloy ingot is hot forged at 1100°C into a 20×20mm billet to provide raw materials suitable for rolling;
[0039] The forged alloys were hot-rolled at 980°C and warm-rolled at 450°C, respectively, and rolled into wire rods with a diameter of 8 mm;
[0040] The wire rod rolled into φ8mm is cold drawn at 10-35°C, and then cold drawn into a φ1.5mm wire.
[0041] Figure 4 .for Fe 76.2 Ga 18 Mn 4 V 1 Ce 0.8 The room temperature magnetostriction curve...
Embodiment 3
[0042] Example 3: Fe 58.5 Ga 17 Ni 20 Cu 2 Ti 3 Dy 0.5 Magnetostrictive filament
[0043] Weigh the raw materials required for the design composition with an electronic balance, in which Fe, 99.99% Ga, 99.5% Ni, 99.9% Cu, Ti, Dy, and 3% Ga, Dy are used. The amount of loss, put the prepared raw materials into the crucible, and vacuum to 3 × 10 -3 Pa, pass argon protection and heating to form an alloy, and after melting, refining for 2 to 3 minutes, and then pouring into an alloy ingot;
[0044] The alloy ingot is hot forged at 1100°C into a 20×20mm billet to provide raw materials suitable for rolling;
[0045] The forged alloys were hot rolled at 1000°C and warm rolled at 450°C, respectively, and rolled into wire rods with a diameter of 6.5 mm;
[0046] The wire rod rolled to φ8mm is cold drawn at 10-35°C, and then cold drawn into a φ1.0mm wire.
[0047] Figure 5 .for Fe 58.5 Ga 17 Ni 20 Cu 2 Ti 3 Dy 0.5 The room temperature magnetostrictive performance curve o...
PUM
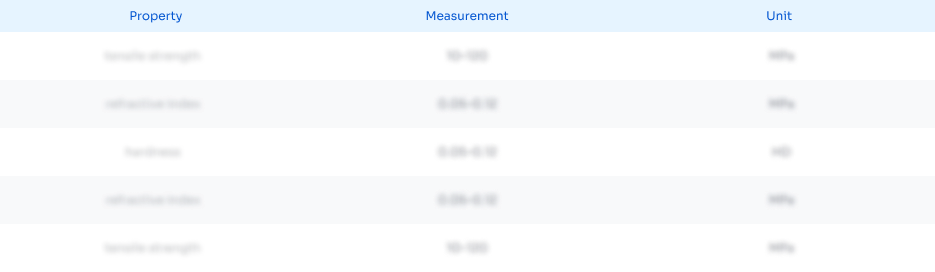
Abstract
Description
Claims
Application Information

- R&D
- Intellectual Property
- Life Sciences
- Materials
- Tech Scout
- Unparalleled Data Quality
- Higher Quality Content
- 60% Fewer Hallucinations
Browse by: Latest US Patents, China's latest patents, Technical Efficacy Thesaurus, Application Domain, Technology Topic, Popular Technical Reports.
© 2025 PatSnap. All rights reserved.Legal|Privacy policy|Modern Slavery Act Transparency Statement|Sitemap|About US| Contact US: help@patsnap.com