Method for generating dimethyldichlorosilance by utilizing disproportionation reaction
A technology of dimethyldichlorosilane and monomethyltrichlorosilane, which is applied in the field of comprehensive utilization of three wastes, can solve the problems of low comprehensive utilization rate of by-products and high energy consumption, and achieves simple and easy operation, low cost and reasonable design. Effect
- Summary
- Abstract
- Description
- Claims
- Application Information
AI Technical Summary
Problems solved by technology
Method used
Examples
Embodiment 1
[0021] This disproportionation reaction should adopt the kettle-type batch operation method. The kettle can be a single unit or multiple units. It is determined according to the effective volume and production scale of the single unit of the stirred tank. The stirring speed should be controlled by frequency conversion.
[0022] Put 10kg of monomethyltrichlorosilane, 5kg of trimethylmonochlorosilane and 0.015kg of catalyst aluminum powder into the high-pressure stirred tank, control the loading coefficient of the stirred tank to not more than 75%, seal all the interfaces on the stirred tank, start the stirring, and stir The speed is controlled at 100r / min, and then the temperature is slowly raised with heat transfer oil to raise the temperature to 180°C, after 1 hour of constant temperature, stop heating, cool to normal temperature, use the residual pressure in the kettle or nitrogen to press the reacted materials out of the stirred kettle After the material is filtered, it enters ...
Embodiment 2
[0025] Put 10kg of monomethyltrichlorosilane, 10kg of trimethylmonochlorosilane and 1kg of catalyst anhydrous aluminum trichloride into the high-pressure stirred tank, control the loading coefficient of the stirred tank to not more than 75%, seal all the interfaces on the stirred tank, and start Stir, the stirring speed is controlled at 200r / min, and then slowly heat up with heat transfer oil to raise the temperature to 250℃. After 3 hours of constant temperature, stop heating and cool to normal temperature. Use the residual pressure in the kettle or nitrogen to pressure the reacted materials Out of the stirred tank, the material is filtered and then enters the organosilicon monomer separation system for separation to obtain 15.76kg of dimethyldichlorosilane, the conversion rate is 78.80%, and the separated high boilers, low boilers and trimethylmonochlorosilane are separated , Monomethyltrichlorosilane continues to be recycled as a principle.
Embodiment 3
[0027] Put 10kg of monomethyltrichlorosilane, 8kg of trimethylchlorosilane and 0.36kg of aluminum powder and anhydrous aluminum trichloride combined catalyst into the high-pressure stirred tank, control the filling coefficient of the stirred tank to not more than 75%, and seal the stirred tank Connect all interfaces, start stirring, control the stirring speed at 300r / min, then slowly raise the temperature with heat transfer oil to raise the temperature to 350℃, after 4 hours of constant temperature, stop heating, cool to normal temperature, use the residual pressure in the kettle or nitrogen The reacted materials are pressed out of the stirred tank, and the materials are filtered and then enter the organosilicon monomer separation system for separation. 11.67kg of dimethyldichlorosilane is obtained, and the conversion rate is 64.83%. The separated high boiling, low boiling and three Methylmonochlorosilane and monomethyltrichlorosilane continue to be recycled as the principle.
PUM
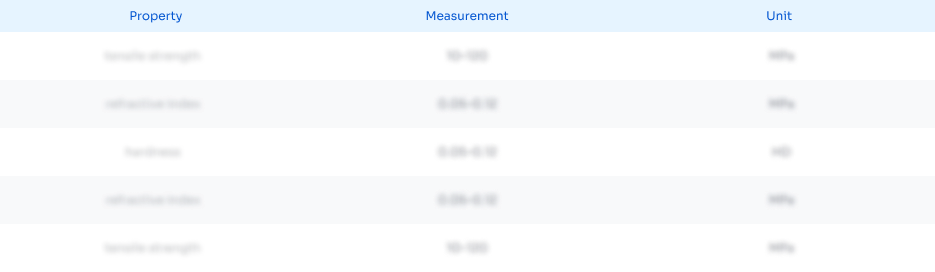
Abstract
Description
Claims
Application Information

- R&D
- Intellectual Property
- Life Sciences
- Materials
- Tech Scout
- Unparalleled Data Quality
- Higher Quality Content
- 60% Fewer Hallucinations
Browse by: Latest US Patents, China's latest patents, Technical Efficacy Thesaurus, Application Domain, Technology Topic, Popular Technical Reports.
© 2025 PatSnap. All rights reserved.Legal|Privacy policy|Modern Slavery Act Transparency Statement|Sitemap|About US| Contact US: help@patsnap.com