Electric power-steering controller
An electric power steering and control device technology, which is applied in the direction of automatic steering control components, power steering mechanisms, electric steering mechanisms, etc., can solve the problems of unable to extract vibration components and suppress vibration components, and achieve the effect of efficient reduction
- Summary
- Abstract
- Description
- Claims
- Application Information
AI Technical Summary
Problems solved by technology
Method used
Image
Examples
Embodiment approach 1
[0025] figure 1 It is a block diagram showing the configuration of the electric power steering control device according to Embodiment 1 of the present invention. In addition, the detailed description of the electric power steering device itself is omitted here, and it may have a known configuration, for example, the configurations described in the above-mentioned Patent Documents 1 and 2 can be referred to.
[0026] In the figure, the steering torque τ0 when the driver steers the steering is detected by a torque sensor 1 using a known torsion bar, and the assisting torque provided by the torque controller 2 to the motor 5 is calculated based on the output of the torque sensor. Moment current Ia. On the other hand, the rotational speed of the motor 5 is detected by a known rotational speed detection unit 7 .
[0027] Next, by having figure 2 The small-amplitude filtering filter 8 having the input-output characteristics shown above filters the rotation speed signal Sn from t...
Embodiment approach 2
[0044] Figure 7 It is a block diagram showing the configuration of the control device according to Embodiment 2 of the present invention. In Embodiment 1, vibration suppression control was performed by applying the small-amplitude extraction filter 8 to the rotational speed signal Sn, but in this embodiment, the small-amplitude extraction filter is applied to the steering torque signal τ0 detected by the torque sensor 1 8 to perform vibration suppression control. exist Figure 7 , with the same designation as the figure 1 the same or equivalent parts.
[0045] In the drawing, a torque sensor 1 detects a steering torque when the driver steers, and an assist torque current Ia is calculated by a torque controller 2 based on a steering torque signal τ0 output from the torque sensor. Next, by having figure 2 The small-amplitude filtering filter 8 having the input-output characteristics shown above filters the steering torque signal τ0 from the torque sensor 1 to remove the s...
PUM
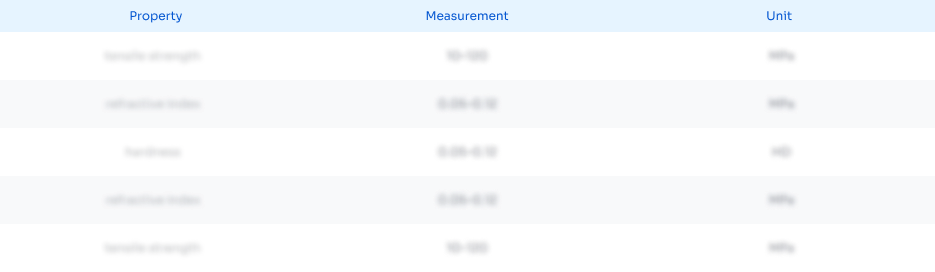
Abstract
Description
Claims
Application Information

- R&D
- Intellectual Property
- Life Sciences
- Materials
- Tech Scout
- Unparalleled Data Quality
- Higher Quality Content
- 60% Fewer Hallucinations
Browse by: Latest US Patents, China's latest patents, Technical Efficacy Thesaurus, Application Domain, Technology Topic, Popular Technical Reports.
© 2025 PatSnap. All rights reserved.Legal|Privacy policy|Modern Slavery Act Transparency Statement|Sitemap|About US| Contact US: help@patsnap.com